Jeep XJ Overland Build Ep06: Box Rockers, Slider Sill Replacement
Description
With the center chassis Stiffener in place I wanted to address the rusted sill/rocker panel as it had quite a few holes in it. Rock/tree sliders were also something I had been wanting to get for some time. So I decided to kill two birds with one stone and cut the rusted sill out and install 2x6 box section and tie this back to the stiffener.
To date the build is almost finished and myself and Megan move out of our home in two weeks and then move into the Jeep. We have our roof tent and a most of the gear and then our journey begins through Europe into Norway and then finally Sweden to a log cabin in the wilderness.
Thanks for watching.
MCQBushcraft:
If your interested in Bushcraft & Survival skills, fishing, hunting, fire lighting, plants & mushrooms, camp cooking, shelter building, self reliance, wilderness & primitive living skills, weaving plant fibers, knives, axes, saws and maintaining these tools in the field and much much more then check out my channel page below for playlists and more videos.
All my Videos:
https://www.youtube.com/user/MCQBushcraft/videos
Become a Patron:
https://www.patreon.com/MCQBushcraft
Check out my Shop for hand made products and more:
http://www.mcqbushcraft.co.uk/shop/
Have a look at my Amazon Stores:
UK Store - http://astore.amazon.co.uk/mcqbushcraft-21
US Store - http://astore.amazon.com/mcq-20
Follow me on Social Media:
Connect On My Website - http://www.MCQBushcraft.co.uk
Connect On Facebook - https://www.facebook.com/MCQBushcraft
Connect On Instagram - http://www.instagram.com/mcqbushcraft1
Connect On Twitter - http://www.twitter.com/MCQBushcraft
Tags: jeep,xj,overland,build,jeep cherokee,4x4,offroad,diy,jeep build,jeep project,jeep xj,xj build,cherokee build,xj project,cherokee project,jeep cherokee xj,camping,cherokee,overlanding,modification,mcqbushcraft jeep build,overland vehicle,off-road,overland build,weld,lift kit,fabrication,custom,rough country,welding,adventure,storage,bumper,4wd,tire,rock slider,trail,suspension,project xj,mcqbushcraft,mcq bushcraft
Video Transcription
hi there guys microphone Sikhi bushcraft here welcome to another episode on the build series in the last video we fitted the rough stuff frame stiffness to the center part of the chassis on the vehicle I haven't done the front yeah it's in this box just behind me here that'll be coming up in future episodes but first we need to finish off the center of the vehicle you saw what I did to the other side I cut out the rusty sill putting two by six box section tied that back to the stiff no which can be directly welded to now because of its thickness and all-in-all I gained a strong of sill without any problem areas that are gonna rust out like the old one and a slider that's tied in to the stiffness so it's a really strong area now on the vehicle but I've got the Box section over here and we're gonna get started with cutting the ceiling and this is what we're looking at here this is the new silvers going to be going in and this is precisely sixty seven and a half inches long from arch to arch right to the end it's a full length replacement and you're looking at collectively a piece of two by six box section bossy giving it a clean down and used weld through primer on it as well well there you can see in my case I've actually got a piece of 2x4 and just put an extra piece on the side just to make it up to two by six and there's a valid reason for that in my case so I wouldn't advise you to it I just go get a piece of two by six to the right length I suppose the positives of having two pieces of box like this as strength you've now got and in a wall that can't be twisted and contorted as easily as if it was just hollow but at the same time the disadvantage is er you've got to make the thing up and wait so it may seem like I'm charging into something pretty sketchy here cutting out a sill on a vehicle and welding in box section it's all pretty extreme but I got my inspiration to do this from Matt's from bleep and Jeep he's got a video where he shows you how to do this as well I was looking for a solution for my rusty sills spotted that video and it's actually quite a common modification a lot of people do this to this particular vehicle it's not just something I'm doing of my own creation you know I've looked at loads of tutorials out there online lots of people have done it so if you are interested in doing this you can always google it and have a look and you'll probably find quite a lot of guidance out there but I'm just going to take this disk cutter and where we're going to cut it's just literally below that lip there I'm probably going to drop down about half a centimetre and cut all the way along and I'm going to leave the plastic arches on for now because I'm actually gonna cut them too [Music]
so I'm underneath the vehicle you can see where I've made a cut along there that's the bottom of the door this is the cell and it's this portion here that we want to be removing this is the flange or pinch weld where two pieces of metal are connected together so as his spot welded all the way along this is the bit that always rocks water gets in between the two pieces of metal there's very little paint in that it's a problem area on a lot of old vehicles and where we're gonna cut is if you see this flat piece of metal here this is the floor pan and this is kind of the beginning of the sill this line here I'm drawing with my finger so what we need to do is go in about half an inch and cut all the way along there like that leaving ourselves just half an inch of metal here to hammer against the box section and weld with
[Applause]
well that's the SIL cutout in the middle is fairly rust-free you can see the dye natural wax line the inside I did that a while ago
and that saved it from getting any worse the front was a little bit tricky to cut because you've got some thick joins in there and bolts but you just have to get through it and put any metal back if you cut too much away the back end is where it's rusty on mine but it's not rusted through and it's still pretty structural and the gauge of Steel is thick enough that it's just surface rust [Music]
[Applause]
[Music]
[Applause]
[Music]
[Applause]
[Music]
so you can see the prat work I've done that we've we've cleaned this lip here that will be directly welded to we've cleaned under here as well this lip there inside has been cleaned up to about there's obvious we don't want the wax dripping down we did have a little bit of pitting and rust at the bottom there but I've just wire brush that I am very aggressively not too fussed about that as this will be pumped full of cavity wax which is a got good rust inhibitors in it anyway so it shouldn't get any worse the back is where the real rust was we were fine on the outside you can see that it's all been cleaned up and looking good but inside here we did have some rust and even a repair that someone had done some time ago so I've just cleaned that up as best I can well the metals still good you know and this is fine it's pretty solid I'm just gonna patch that up with some filler I'm not particularly too worried about it I may have to come back to it in years to come but for the time being you'll be okay so that's about each corner and we've got just past an inch protrusion past the doors and that isn't really a lot you'd be better off of something like 2 by 8 and a lot of people usually recommend that 2 by 6 is okay though and what I intend to do is actually get some tubing and have it coming out in other two inches all the way along here and bending back in and the support in the middle and that was the long term goal whether we'll do that before the trip I don't know maybe I'll have to do it after but for the time being this is obviously a strong base to then work from which is the reason I'm doing it so we're gonna get this tack welded in there and then start hammering metal back underneath that we've bent back and then tack weld that in as well so you can see what I've done there I've hammered back that lip we created just to make it flush it needs hitting again in a couple of places before we weld it in permanently
[Music]
I've spot-welded it in and we're ready to weld this on now and I've just started my first weld here started off a little bit ropey started blowing some holes in it found it a bit difficult actually if I managed to get things it's kind of progress a bit better so I'll carry on welding this in and hopefully as we go through it I can improve a bit [Music]
[Music]
well the new sale or the slider is welded him I couldn't film too much of that it's very challenging I found that pretty difficult I don't do too bad while I'm on the bench and I've got two pieces of metal in front of me and they're thick it's not as difficult but you're welding a three mil piece of box section to a really thin body panel and the way I was taught as you focus on the thick metal and then gradually pull into the thinner metal and that worked a lot of the time but sometimes it just wouldn't flow right and it would get really spitty
I don't know whether it's just this world through primer which I mean maybe it isn't or maybe it's just me maybe I'm just not that good at welding but I had some good runs and overall it's structural I've continuously welded all the way along here into the front arch into the rear arch and all the way along the bottom so we'll get those legs made and then I hide my shame with p38 [Applause]
[Music]
[Applause]
[Music]
so all four supports are installed I had to build some half-inch spaces for the two supports at the front simply because the chassis moves it like an S bend the floor pan Sachs Bank in certain areas they're not all gonna go in the same way and they've all come out quite well I've got two fairly close together at the front and then to a little bit more spaced apart the back to match the other side and that's kind of how I want them to be and you're not actually going to see them anyway because we're gonna have a skid plate underneath here eventually prior to about a splash plate made of aluminium that will cover them up but I've cleaned all this down now with degreaser and I'm ready to use p-38 which is a filler to basically protect all of the wells or hide them in my case and do the same underneath and it just means that much like the other side it almost looks like it's come from the factory
[Applause]
so I finished using seam sealer and p38 I like to use the seam sealer first because it's a lot thinner it's more like a grease whether it's p-38s like almost like clay and it's gone on nicely and this needs the harden now I'll come back tomorrow check it out and then we'll see if we can prime and paint it we're a few days on from when the filler and the seam sealer were applied and I left it about three days made sure it was completely dry and then sanded it down smooth and then Zink primed the whole area even the filler any bare metals been zinc primed underneath all the legs have been zinc Prime's and then I let that set for about a day and a half and then satin black the whole thing and then just while the satin black was tacky I used a bed liner just to give the satin black a bit of texture you remember in the last videos while we used the dinner trowel cavity wax hose with the diffuser on the end with the remaining holes along the top that all seemed to be filled I used the cavity wax hose in there and filled the whole sill and lined it with cavity wax so all the bare metal in there will be covered now but I had some spare aluminium and I decided to take that aluminium to the fabricators and get them to put a 45 degree ban just on the edge of it I made like a splash plate just to go underneath the actual vehicle but the idea of this was just to stop lots of mud and grit and all sorts of rubbish getting up into those supports and basically hitting the bottom of the undercoat on the floor pan and gradually wearing it away so it just protects that investment I've just put into all of that section just there and the way you fit that splash pan is obviously quite important I've got it separated with half inch and one-inch spaces so it actually mounts under the vehicle a slight slant like that and there's a gap just between the actual sill and the splash plate so I can see down into it get the pressure washer in there just blast anything out and I left a gap between the actual splash plate and where the frame and so it means that everything can just run down and drop a I've tied it into the front mud flap I've also extended the rear DIY wheel well so that can x2 like a kind of splash plate as well that wraps around the underneath of the aluminium plate and it means it's fully protected and we'll see how it does hopefully it'll be okay but my advice to people who would be building a vehicle like this for a rock crawling purpose may be out in the States a lot of people rock crawl of Cherokees I'd say that I would just wouldn't bother with any of that and probably even do a different design of the actual supports that I've made because you know they're just gonna get hung up on rocks you probably just want to main a half inch thick plate like this from the sill to the frame so it acts as a skid plate but also supports the two pieces together so they tied together nicely but it's all looking real good and I've undertaken another massive project now once this is done a friend of Mines helping with the set of drawers in the back and some shelving and a table that will come out the back we've got all the gear we've got the stove so I've got a new suspension to go in new shocks I've got strength and steering arms I've got to redo all the bearings I've got new joints to put in some of this I'm not going to be able to film and as some of you are interested in this build others probably not in fact the most of people who watch my child probably aren't but um it is a part of the process and we're gonna be living in this for six months and we move out of our home in two weeks I mean our possessions have basically been reduced down to a few boxes and everything else has gone to charity shops and we've sold it so you know it's kind of amounting up and it says weighing on top of me a little bit actually I'm starting to think what the hell am i doing and megan is as well but it should be an exciting trip and you know it's just the sense of freedom being on the road and the jeep we've got the roof tents actually in the back of the Jeep say we'll see how it goes but you can see the front there the vehicle it's all stripped down ready for the front frame stiffener and I'll get that sorted and then get the front rebuilt and then the vehicle is pretty much almost ready so I hope you enjoyed this video I appreciate you watching and I'll see you very soon another one take care guys thanks again you
About the Author
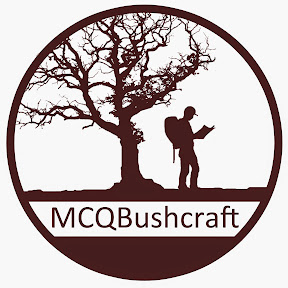
MCQBushcraft
I'm a UK based outdoorsman who started hunting and fishing with my friends when I was young.
Educating yourself about your surroundings and having the core skills to sustain yourself using your environment is a lost curriculum in the United Kingdom. We are well provided for, so well that "why do anything if somebody else will do it for you". This lifestyle has drastically disconnected people from having the knowledge and skills required to spend even one night in the woods and not get hungry.
I love being outdoors and have never lost the desire to learn and practice skills that I get a sense of natural connection from. Hunting hangs controversy in the minds of many, but in my eyes there is nothing more natural if you choose to eat meat. I appreciate that not everybody hunts in moderation though.
Thanks for reading
Michael McQuilton
Private Sponsorships: http://fbit.co/u/MCQBushcraft
More articles from this author
- Bushcraft Containers: Pine Pitch & Spruce Cord
- Bushcraft Basics Ep06: Choosing a Backpack
- Hunting: Pigeon Shooting with a Shotgun
- Bushcraft Basics Ep12: Knife Safety
- Bushcraft Basics Ep15: Personal Med Kit
- Bushcraft Shelters: Hammock & Tarp Setup
- MCQBushcraft 2015 Channel Update
- MCQBushcraft Q&A: Ep01 - About Me
- Bushcraft Fire Lighting: Leather Tinder Pouch
- Wild Camping & Bushcraft with ZedOutdoors
- Bushcraft Basics Ep10: UK Knife Law
- Field Dressing a Brown Hare
- Bushcraft Basics Ep20: Making Fire Feather Sticks
- Bushcraft Fire Lighting: Cramp Ball Fungi
- Bushcraft Equipment: The Hidden Woodsmen
- Bushcraft Fire Lighting: Woodburning Stoves
- Bushcraft Shelters: Quick Deployment Tarp System
- Bushcraft Equipment: Maxpedition Condor II Pack
- Bushcraft Basics Ep13 - Knife Maintenance
- Hunting: Shotgun on Pigeon & Rabbit (Two Day)
- Field Dressing Game: Duck Whole Bird
- 200,000 Subscriber Giveaway Prize Draw Winners!
- Solo Three Day Hunting & Bushcraft
- Solo Five Day Hunting & Bushcraft
- Bushcraft Containers: Frying Pan
- Bushcraft Foraging: Dehydrating Mushrooms
- Field Dressing Game: Pheasant Breast Only
- Wood Carving & Crafts: Bushcraft Tinder, Skulls, Knives, Carvings & Furs
- Bushcraft Foraging: Piptoporus Betulinus
- Wood Carving & Crafts: Tinder Pouches & Leatherwork
- Bushcraft Fire Lighting: Using a Firesteel
- Bushcraft Camping: The Lake District
- Hunting: Slingshot Aiming Techniques (Aimed)
- Hunting: Grey Squirrels with a Shotgun
- Bushcraft Equipment: 'Old Kit' September 2013
- Bushcraft Foraging: Pignuts
- Camp Cooking: Crayfish
- Wood Carving & Crafts: Alder Spoon & Kuksa
- Coastal Bushcraft: Two Days Fishing & Camping
- Bushcraft Foraging: Alexanders
- MCQBushcraft Hunting & Shooting Compilation
- Shooting Gear: My Game Bag & Goose Gun
- Bushcraft Knives: ESEE Izula II Firesteel
- Bushcraft Camping & Cooking on Embers
- Hunting: Slingshot Aiming Techniques (Intuitive)
- Bushcraft Fire Lighting: Fire Kit & Bowdrill
- Camp Cooking: Roasting Pheasant over a Fire
- Wood Carving & Crafts: English Yew ladle
- Bushcraft Foraging: Saffron Milk Cap
- Bushcraft Fire Lighting: Introduction
- Shotguns & Hunting Gear
- Hunting: Grey Squirrel & Woodpigeon
- Bushcraft Basics Ep05: Land Access Northern Ireland
- Bushcraft Sweden: Ep05 - Four Days Canoeing In The Wilderness
- Bushcraft Foraging: St George's Mushroom
- Bushcraft Basics Ep16: Field Journal
- Bushcraft Basics Ep08: Water Contaminants & Pathogens
- Bushcraft Foraging: Wild Edibles of Spring
- Bushcraft Fire Lighting: Finding Fatwood Heart Root Tinder
- Bushcraft Knives: ESEE 90 Degree Spine
- Bushcraft Knives: Using Animal Fats
- Bushcraft Shelters: Weaving a Grass Bed
- Bushcraft Basics Ep03: Open Access Land England & Wales
- Bushcraft Knives: ESEE Paracord Sheath
- Bushcraft Sweden: Ep02 - Cliff Top Camp
- Bushcraft Foraging in the Woodland
- Bushcraft Fishing: Using a Hobo Reel
- Bushcraft Knives: Camp Knife & Neck Knife
- Bushcraft Basics Ep19: Finding Fatwood Tinder
- Bushcraft Equipment: My Gear & How To Use It.
- Bushcraft Basics Ep07: Water Containers
- Jeep XJ Off Road Crayfish Recovery
- Bushcraft Foraging: Tapping Birch Water
- Bushcraft Foraging: Dryads Saddle Mushroom
- Bushcraft Basics Ep02: Private Land England & Wales
- Hunting: Pheasant & Wood Pigeon
- Bushcraft Basics Ep18: Ferrocerium Rod Technique
- MCQBushcraft Q&A: Channel Update 2016
- Bushcraft Equipment: Maxpedition Xantha
- Bushcraft Sweden: Ep01 - Gear Overview
- Bushcraft Foraging: Navelwort
- Bushcraft Sweden: Ep04 - Hunting Capercaillie & Black Grouse
- Bushcraft Knives: Jacklore Knives
- Bushcraft Sweden: Ep03 - Canoeing & Fishing In The Wilderness
- Bushcraft Basics Ep14: Knife Sharpening
- Bushcraft Camping: Woodland Wild Camp
- Bushcraft Basics Ep04: Land Access Scotland
- Bushcraft Containers: Pot Hangers
- Bushcraft Fire Lighting: Finding Fatwood Pine Shoulder Tinder
- Bushcraft Basics Ep09: Water Filtration & Disinfection
- Bushcraft Clothing: Outdoor Clothing & Layering
- Bushcraft Clothing: Deerhunter Waterproofs
- Bushcraft Foraging: Hawthorn Fruit Leather
- Bushcraft Fire Lighting: Fly Repellent
- Field Dressing Game: Pheasant Whole Bird
- Essential Knots: Bushcraft & Tarp Setups
- Bushcraft Basics Ep17: Fire Lighting Tools
- 200,000 Subscriber Giveaway Entry Video (CLOSED)
- Field Dressing Game: Rabbit for Meat & Fur
- Wood Carving & Crafts: Bushcraft Fire Lighting Set
- Bushcraft Foraging: Tapping Birch Water (tree friendly)
- Bushcraft Foraging: Hairy Bittercress
- MCQBushcraft Q&A: Channel Update 2017
- Bushcraft Basics Ep11: Bushcraft Knives
- Bushcraft Fire Lighting: Essential Technique of Bow Drill Friction Fire
- Bushcraft Foraging: Ramsons
- Clay Pigeons Shooting With The Knife Makers
- Bushcraft Foraging: Seasonal Edibles Ramsons
- Foraging & Cooking Dryad's Saddle
- Bushcraft Foraging: Wild Edibles of Summer
- Coastal Bushcraft: Trotline Fishing
- Field Dressing Game: Grey Squirrel
- Bushcraft Axe Work: Sharpening
- Bushcraft Fire Lighting: Tinder Fungus
- Hunting: Wood Pigeon & Grey Squirrel
- Coastal Bushcraft: Foraging & Cooking Shellfish
- Bushcraft Axe Work: Safety & Technique
- Bushcraft Knives: Field Sharpening & Stropping Kit
- Bushcraft Equipment: Swedish LK35 Backpack
- A Windy Day Hunting Wood Pigeons
- Bushcraft Basics Ep01: Introduction
- Bushcraft Knives: The Field Master
- Hunting: Slingshot on Grey Squirrel
- Bushcraft Equipment: Catapult Target Practice
- 200,000 Subscriber Giveaway Announcement
- Hunting: Wood Pigeons Early December
- Bushcraft Containers: Basket Weaving, Clematis
- Bushcraft Equipment: Full Kit July 2014
- Bushcraft Shelters: Camp Construction
- Bushcraft Axe Work: Leather Collar
- Bushcraft Containers: Washing & Sterilising
- Field Dressing Game: Wood Pigeon
- Bushcraft Foraging: Lesser Celandine
- Bushcraft Fire Lighting: Make Fire With Fatwood Tinder
- Wood Pigeon Decoying Over Maize Stubble
- Bushcraft Basics Ep21: Choosing a Bushcraft Saw
- Part 1: Fitting a Wood Burning Stove to a Canvas Bell Tent
- My Experiences on YouTube & Plans for 2018
- Part 2: Fitting a Wood Burning Stove to a Canvas Bell Tent
- Jeep XJ Overland Build Ep02: Workshop & Tools
- Jeep XJ Overland Build Ep01: Vehicle Overview
- Winter Bivi Camping & Cooking Wood Pigeon Curry
- Jeep XJ Overland Build Ep03: Rear Bumper Upgrade, Sliders & Tie Ins
- Traveling Northern Europe 4x4 Ep02: Our Journey & Living in a Jeep
- Jeep XJ Overland Build Ep05: Ruffstuff Frame Stiffeners Install
- Traveling Northern Europe 4x4 Ep08: Rooftop Tent Camping Norway - Part 4
- Jeep XJ Overland Build Ep04: Tyre Carrier, Bumper Supports & Rear Stiffeners
- Traveling Northern Europe 4x4 Ep04: Rooftop Tent Camping Denmark
- Traveling Northern Europe 4x4 Ep07: Rooftop Tent Camping Norway - Part 3
- Traveling Northern Europe 4x4 Ep05: Rooftop Tent Camping Norway - Part 1
- Traveling Northern Europe 4x4 Ep06: Rooftop Tent Camping Norway - Part 2
- Traveling Northern Europe 4x4 Ep03: Rooftop Tent Camping North West Germany
- Offroad Truck Camper Build Ep07: Ruffstuff Front Stiffeners & Front Axle Overhaul
- The end of MCQBushcraft as we know it.......
- Traveling Northern Europe 4x4 Ep01: Rooftop Tent Camping The Netherlands
- MCQBushcraft Traveling Europe 4x4 Ep09: Finding our New Home in Sweden
- Campfire Cooking 'Show us your Steak' Men's Mental Health