Primitive Technology: Natural Draft Furnace
Description
I built a natural draft furnace to test ideas about how hot a furnace could get without the use of bellows. Natural draft is the flow of air through a furnace due to rising hot air. The hot gasses in the fuel bed are more buoyant than the cold air outside the furnace causing them to rise. Fresh combustion air then enters the base of the furnace to replace the rising combustion gasses, keeping the fuel bed burning. This effect increases with: 1. the average temperature of the fuel bed relative to the outside air and 2. The height of the furnace. Two other important factors are the size of the tuyere (air entry pipe) and lump size of the fuel bed as these effect the resistance to airflow through the furnace. The furnace was tested with wood fuel and some ore was melted but produced no iron. High temperature were indeed produced (probably about 1200 c). These types of furnaces were once used for smelting copper and iron ores in around the world in ancient times, usually using charcoal as a fuel and in some cases wood too.
I designed the furnace using a formula from the book “The mastery and uses of fire in antiquity” by J.E. Rehder. It was designed to have a space velocity (air speed within the furnace) of 6 m per minute which is recommended for iron smelting. The furnace was 175 cm in total height but with a height of only 150 cm above the tuyere. The height between the air entry and the top of the furnace is what determines the strength of the draft, the space beneath the air entry is not included in the formula. The internal furnace diameter was 25 cm. The walls were about 12.5 cm thick at the base but got thinner with height. The tuyere (air entry pipe) was 7.5 cm internal diameter and about 20 cm long. The tuyere was placed into an opening in the base of the furnace and sealed with mud. The whole thing took about a week to make due to the slow drying time that was assisted by keeping a fire burning in side it. The furnace was designed to use charcoal (which in this case should be 2.5 cm diameter lumps) but I used wood to test it instead as it was easier to acquire. To test its melting ability, bog ore was found further down the creek and roasted. The roasted ore was then crushed and stored in a pot.
The furnace was filled with wood and lit from the top. The fire burnt down the furnace producing charcoal. On reaching the tuyere the fire then started burning the charcoal. Wood was also continually added from the top along with a few small handfuls of the roasted bog ore (not shown in the video). The temperature of hot objects can be visually estimated from their incandescence. After about an hour, the light coming out of the tuyere was high yellow to white hot indicating a temperature of at about 1200 c. Colour temperature charts vary but white hot is usually given to be at least 1200 c, examples of these charts can be found on the internet for reference. It was uncomfortable to stare into the tuyere and doing so left an after image when looking away, indicating the strength of its brightness. After about an hour and a half the furnace was left to burn out. When opened the next day the tuyere was covered in slag with bits of slag found on the furnace floor also.
This experiment shows that high temperatures can be achieved without the use of bellows or charcoal, which might significantly reduce labour in the production of iron. The furnace was technically easy to build as it was a simple vertical cylinder. When running, the wood added to the top of the furnace converts to charcoal in the upper part of the stack and is consumed in the lower part. The ore I used was new to me, normally I use iron bacteria as an ore. This new ore produced no metallic iron so I’m inclined to use iron bacteria in future. Natural draft furnaces were once used to smelt copper and iron ores in the past, usually with charcoal fuel and less frequently with wood. The main benefit of these furnaces seems to have been the reduction in labour they provide and simplified infrastructure (fewer workers and no bellows required during operation).
Video Transcription
Digging base
Stone floor to prevent rising damp Harvesting termite clay Mixing clay
Palm leaves for fiber Floor layer
Furnace wall
Internal diameter 25 cm Drying layer out Bridge over door way with sticks Clay over sticks I could do about 5 layers a day due to the slow drying of the clay It's important not to rush building the furnace or it will slump Only add new clay when the last layer has stiffened Total height 175 cm, time taken 7 days. Making tuyere (air pipe) from clay. Inner diameter 7.5 cm Blocking up doorway Positioning tuyere at 15 degree downward angle Tuyere nose sticks into furnace Bog ore formation about 1 km further down the creek Ore roasting
Crushing ore to a powder Wood for the furnace (no charcoal was used in this experiment) Furnace stacked and lit from the top The tall furnace draws a strong natural draft. Adding wood and ore Fuel bed can be seen through the tuyere. Estimated at least 1200 c if not higher. After an hour and a half total, it was left to burn down. The next day the tuyere was seen to have been covered with slag (no metallic iron though) Slag from the bottom of the furnace The slag was magnetic but had no metalic iron Natural draft furnace
About the Author
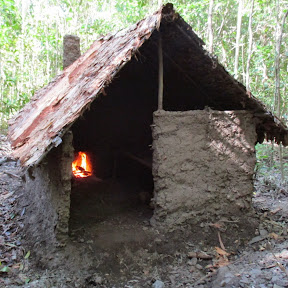
Primitive Technology
Making primitive huts and tools from scratch using only natural materials in the wild.I also have this blog:
https://primitivetechnology.wordpress.com/ (I have no facebook page- ignore the fakes)
FAQ
Q.Where is this?
A.This is in Far North Queensland Australia.
Q.Do you live in the wild?
A.I don't live in the wild but just go into the bush to make these projects. Also I camp out here occasionally.
Q.How did you learn all this?
A.Researching books and internet plus trial and error. I'm not indigenous and have no army training.
Q.What about dangerous animals in Australia?
A.The only really dangerous ones in my area are snakes. Care must be taken when walking about and lifting things from the ground.
Q.For the mud huts what stops the rain washing the mud walls away?
A.The roof.
Q.Why don't you talk in the videos?
A.When I watch how to videos I fast forward past the talking part to see the action part. So I leave it out of my videos in favor of pure demonstration.
More articles from this author
- Primitive Technology: Stone Adze
- Primitive Technology: Palm Thatched Mud Hut
- Primitive Technology: Spear Thrower
- Primitive Technology: Making poisonous Black bean safe to eat (Moreton Bay Chestnut)
- Primitive Technology: Chimney and pots
- Primitive Technology: Termite clay kiln & pottery
- Primitive Technology: Planting Cassava and Yams
- Primitive Technology: Woven bark fiber
- Primitive Technology: Sling
- Primitive Technology: Forge Blower
- Primitive Technology: Stone Axe (celt)
- Primitive Technology: Wattle and Daub Hut
- Primitive Technology: Firesticks
- Primitive Technology: Charcoal
- Primitive Technology: Sandals
- Primitive Technology: Reusable charcoal mound
- Primitive Technology: Wood shed and Native bee honey
- Primitive Technology: Simplified blower and furnace experiments
- Primitive Technology: Tiled Roof Hut
- Primitive Technology: Mud Bricks
- Primitive Technology: Bow and Arrow
- Primitive Technology: Freshwater Prawn Trap
- Primitive Technology: Water powered hammer (Monjolo)
- Primitive Technology: Cord drill and Pump drill
- Primitive Technology: Barrel Tiled Shed
- Primitive Technology: Sweet potato patch
- Primitive Technology: Thatched Dome Hut
- Primitive Technology: Baskets and stone hatchet
- Primitive Technology: Grass hut
- Primitive Technology: Bed Shed
- Primitive Technology: Round hut
- Primitive Technology: New area starting from scratch
- Primitive Technology: Pottery and Stove
- Primitive Technology: A-frame hut
- Primitive Technology: Lime
- Primitive Technology: Yam, cultivate and cook
- Primitive Technology: Blower and charcoal
- Primitive Technology: Wood Ash Cement
- Primitive Technology: Iron prills
- Primitive Technology: Pit and chimney furnace