Glass blowing demo by Ohio City Glass -Mantis Outdoors
Description
Well this is a little different than the usual videos that are on my channel. that being said I am a student of history and I enjoy the art of glass blowing and the history involved. So we asked the guys at ohio city glass to give us a little demo of glass blowing and talk a little about there company and what they do
www.mantisoutdoorsllc.com
This email address is being protected from spambots. You need JavaScript enabled to view it.
Tags: survival,bushcraft,woodcraft,survival kit,outdoors,knife,camping,gear,primitive,skills,mantis outdoors,preparedmind101,william myers,family,education,preparedness,wilderness,woods,Glassblowing (Professional Field),Glass (Visual Art Medium),Ohio City (Neighborhood),Survival (Multipart TV Episode)
Video Transcription
hey guys doing on William Byars mass outdoors today grab the circle go funky show and today we walk back at a really cool food in order to show it to you guys to discuss some very interesting historical facts we conclude in it talking about the Ohio sea glass company on Cleveland Ohio and we're going to get some explanations a little bit of demos about what has changed what hasn't changed and do little demos about glassblowing and a little talk about the history involved in there which they who you are what yeah hi my name is Daniel I'm the owner I've run this studio I do a lot of production work I've been doing this for 10 years or so so you know we have a lot of fun doing what we're doing yeah but it's a lot of work and you'll see here we have to work through the clinic for the fast again we're professional pyromania actually worth of fire always have they loved it so do we so we will share at that joy with you guys so let's go over here and see a little bit demo of what they do like I said I'm here at the Ohio circleville funky show and we're at Ohio City glass boots and right now Daniels will talk about some of the tools they use how much they have changed and now exactly how much they haven't changed from a long long time ago centuries last load game Yeah right hello right now we have the main center the folks here is the mounting first this actually melts the glass so we can work with it over the years that people built furnaces and kill them with many different things would we right now we use propane I use natural gas back at my own shop this thing is pretty much been the focus of how technology has changed guess most of the first is now our computer control a lot of people are going to electric now actually so there's no but for what I do for the portability I use a gas furnace and very rudimentary was only air and gas control pretty much the way started to begin with other than that we've got right over here the newer that actually helps cool the glass down very slowly so doesn't break that's another thing that's evolved a lot over time again computer control with the advent of computer technology that's controlled a lot better by suitable so absolutely flow yes it can't just sit out it'll shadow brave the glass to sit down the air as glass cools it shrinks so you have thick part synthetic drugs and they start to shrink right well against each other and that close to the glass to break so to keep something one piece we actually have to pull it down over about nine hours after it's made so this was a hundred years ago we would have an electric kiln how EA they was back in the day as we say you know they would have a section set connected to the gas kiln that melted the furnace that would be at a lower temperature than they would just shut it down or close it off somehow so that it can cool down slowly very slowly nobody and then they would have a lot of breakage because it's not going slow enough but today we're lucky to have computers that can do all that fancy word for us I just push buttons and it happens this is the main so what kind of temperature you get on the great now we're talking about 2100 degrees inside that man just give or take 100 again it's so hot at 100 degrees in give or take a hundred as that it doesn't matter wes is that a molten state inside the furnace obviously can't just reach my hand in the ground so this is another thing that has not changed working on steel or metal some kind of metal pipes that's going to allow me to blow into the glasses follow this is blowpipe if we watched wad you solid glass a solid rod called upon team without inside here I love you can see with the camera there you have a big bowl that just holds molten glass and a puddle okay so if we take this rod and we'll set it down on the edge of that bowl and then go down into the liquid glass and wrap it around the end of the run so right now you're grabbing glass right now is Fleck honey on the end of a stick hey don't buy that rotation I could get a nice even layer now this is just clear glass you can see it's glowing bright orange again this over 2,000 degrees very hot
and gravity's our master my hang it down grab he's going to pull it off so I'm constantly moving to keep it on center okay now while it's still hot in the center if I blow a little bit you'll see it pushes that hot glass out of the way and now I have a bubble now I've made a piece of blown glass now glass is incredibly flexible warm so that you think nice
so that's a little bit of glass now has been blown out can be big thing bubble is too cheap very fragile now that's so thin that cools down almost instantly so I can grab it this we're just going to show you how flexible the glass actually is like feels like cellophane now you can almost bend it in half okay awesome once I get the glass we can't touch it to shaping so we use metal tools now these dolls are staying pretty much unchanged including the bench when you're working with the glass you sit down to the bench you have two rails to roll pipercross your left hand is always the one through the pipe and the right hand is for the tool get straight razors you can pull little things out of the glass we have cutting tools so you can actually take to cut chunks out of the glass well then of course so the tools that you're using right now hasn't really changed very much over the same pretty much the same the only thing has changed the technology that makes it so we have finer machining technology nowadays but this used to make license last to stretch it out here we can't touch it so anything is one paper with has to be made out of metal but one of the most common tools this is fairly recent is a stack of wet newspaper because I can use this just like all my hand she runs exactly jump that so get anything we make start same thing is gathering the glass out of the furnace
and as I was saying stack my newspaper shields are and from the heat and because its web that water instantly turns II steam contact and creates a barrier between the glass and paper so we won't stay together and that allows me to shave the glass almost as if the Gospels very quickly again it's over 2,000 degrees fresh out of the furnace and he's taking you know 60 70 degrees outside right now so very quickly we'll set up you can see it starts to lose that glow start to get stiffer on the outside
hi I'm SAP craycraft on I work underneath damn who you just saw earlier um I'm just gonna sit down kind of explain some tools to you um right here we got the tweezers pretty pretty simple just two pieces of metal with a nice little bin for a spring used for clamping the glass twisting the glass kind of move it around manipulating it this is really 10 tools that you put real pressure on the glass with and then beside that we have our jacks they have these two roll blades it'll the ones we use actually have two little grooves down the side um these have to be kind of lubricated with wax the whole time you're using them so they don't grip the glass those lines kind of help it meltdown when you lose it on the tips these are used for cutting our lines when we're working on it mostly to break it off the rod kind of get some shaping in Ripton too we also have just straight shooters just like pretty much like scissors that you would have at your house um they have a little bit more of an arm to them so you're not getting all up in the heat burning yourself and then you also have the Diamonds years now these are one of my favorites you can kind of crimp the glass around the neckline I'll help break it off it also has a nice little holder right here so you can grab the hot into the pipe when you get into more heavy work or when you're guiding small bit soft away from where
I mean everyone has their own oil tools that they use I like used actually just a meat cleaver kind of like a paddle kind of flattened some different sections with it and then I also have a dolt out chef's knife I use for sculpting cutting lines in law mostly with solid sculptures like my birds and stuff like that the newspaper which us all shaking down and then oh just open v8 bottle I used to squirt water on just cool them down we also will use a little concrete spreader just kind of like and use that a little more than the item or the fan of the cleaver those are really most of the tools that we use on when we're working on the glass beyond that I don't really get and too many different things I got it I got a couple extra like wool rods and stuff for wrapping it's pretty much it with that with the tools ok so the tools that you explained right now how much have they changed over the centuries decades years I mean with the diamond shares they have the addition of the pipe grabber which is kind of new you have other other versions though I know that there's a check diamond share whether it doesn't have the pipe grab because some people find it gets in the way when you're working on it kind of you kind of have to hold it all the way out on your knuckles otherwise if you try to open it up it doesn't want to open up some people referred and not have a pipe grabber arm I've also seen some that are kind of dumb filled out on the sides it just keeps the glass I'm curling back around on you during trimming so basically the the improvised tools that you have other than those a glass blower from 100 years ago come here and feel right at home yes exactly pretty much um nothing else is really changed I mean anything that we do today it all follows the rules that were laid out by people before us you can always when you're coming up with new things just take something that somebody used to do combined it with some other throw your player on it once you know what you're doing what you know how the glass moves and you know if I find a tool I like if I see something in like a thrift store that I think could be useful I'll grab it I'll test it out and always trying to cope with new things to do always improvise new different ways to kind of move forwards in glassblowing awesome awesome all right right so now we're back here with Daniel and he's going to do a little bit of a ploy demonstration for us right now so Daniels wait a little bit what you're doing all right now I'm actually gonna start by getting some glass out of the furnace crap you the boss around just like hunting on the end of the stick listen to some of these powder colors and those powdered glasses are just going to stand great to the outside because as the heat transfers kind of thick hot sticks too hot but you stick together and we can use that throughout the process to layer colors in different ways to make different effects so all these is powdered glass now as the glass heats up it's dark outside zalgo look Reds all going to be glowing is so high so we have to kind of remember what colors were working with especially right now we're not going to be able to see them so now that I've got a good coating I'm going to eat that in real quick
neither the furnace to melt that glass on the surface now I'm continually tourney because gravity is wanting to pull the glass down by turning that's keeping it up on the end of the pipe kind of like something in orbit now you can see it all this orange again is it glowing and while the center is still really hot molten i'm going to start blowing into it and you'll see there and start to make a public I'm going to be coating this with more glass so I don't want to make the bubble too big or too thin the heat from the fresh glass is going to go over top fixing overheat it he's now I've set my shape I have my bubble established i'm just going to let it cool down now it does come from the outside in shaking on the steel tables hold it very quickly so you'll hear that glass is some wandering out well over a thousand degrees still so when i say cool told us a relative term and what huge
I want to let this cool down to a point where
it's cold enough that I can get more glass on it without it getting too hot and start to move around on me applaud note that it's not going to crack from that sub temperature change so if you were just to glut that state and the ambient area which is crack correct as the glass is cooling the shrinking it shrinks waiting to quickly pulling in the air and that will cause the glass
there's a lot of physics and thermal dynamics involved in glassblowing pizza right now you can see that glow is kind of gone you came to see the metal glowing anymore it is solid but still well over 900 degrees the back down in the glass covering the whole thing as you can see I have much more material now we're going to have a layer of fresh hot clear glass so it all looks kind of porridge and I want to go back and get some more color so all this is just powdered glass outer glass correct we have a cover glass in different forms whether it's a powder or little chunks we buy the colors from a company that makes them Salt Lake paint can't miss you know blue and yellow is speckle have green these are all made of chemicals the metal oxide and then reacted differently with each other's it's easier to buy the color for today I'm he the color back in and then going to a second color now this color is a dark green but when it's hot is softer as we like to say which means that it moves easier at the same temperature so it will spread out over the top of that other color which must improve as much that creates a nice little effect and once see you there well drop it in this mold this is called an optic mold you can see maybe the triangular ribs and I'll blow into that then the glass will take the form of that mole okay that's going to start to set up the pumpkin shape I'm swinging it to stretch it off the pipe a little bit I'll start to blow it out I don't want to finish blowing it out yet so watch how I work with a blow hose so i can actually blow into the pipe while i'm sitting down
all right there right here
so now I'll start to blow it out now again I can't touch the glass so any shape he is done with metal tools upgrading a constriction off the pipe right now
I construction give you a weak point where I can break this glass off plate turn it around insert the opening I'm working very quickly because the glass cool down very fast I'll let it go too much even crack trick so we have to always keep it hot work we're back 13 a little bit taller so whole thing up and then kind of swing it comes dress it out
okay see up swinging it got longer grab you'll also just helped pull it if I want it straight up and down again I'm working to the material that I can't touch
so as I'm working with this the bottom of the bubble becomes the bottom of whatever i'm making now making a cup so imagine the bottom of the bubble is the bottom for cup what we need Fabolous stable base to sit on so I'm just going to beat the very bottom and create a flat spot
he's gonna push the bottom in you can see now to this platform I've got one more thing to do to this before we transfer it to another rod because they shaped the top we actually have to separate it from blowpipe I made a little bit of a flat spot on one side
making sure things where one flattening the wall not making sure I've got this flat spot on the side and possibly pay attention making sure I gave you the whole thing more when I say warm I mean like 1,300 1,500 degrees I don't know exactly what temperature it is the from juniors for 10 years side let's actor this for me while I get another broad ready but grab a solid rod through a little bit of glass in man we call this process the trace for transfer or the punty the uhg why all use a little bit of glass on the end of another rod no hot glass and stick out of there na class so I can attach these two together
very carefully make sure I'm on center okay lots of compassion to the rock I can break away from the pipe even a vibration on the pipe like that I've created that weak spot you can all see now there's a whole okay that's going to be the opening of the cup but that's just fall you want to make it bigger so I'll get up that way it out I'm just focusing on heating the front part of the cup that was the coldest spot now we want that to be the hottest spot so it takes some time
working outside is always interesting especially at night because everything lost a little bit hotter at night colder during the day you'll see the glassblowing when I come out
so once it's hot enough I can kind of age by how much is movie go back to the back see that the rest of it I come in with this tool again like two little fingers start to pull down is a journey and stretch that into an opening now I can flare it out by changing the angle of the tool but I want to keep that flat side right there because that's where it's going to set down this is going to be a pumpkin-shaped mug or pumpkin deemed mug so we want to have this one flat spot because the stem or the handle is going to go on the other side as I'm adding the stem if I don't have a flat spot the whole thing will start to roll around on that's pretty much it the bottom of the body of the bug is made now I want to break this off of this rock right behind you you come off to our cock rock stations here
couple times nice vibration on the rod cost Brinkerhoff now I'm over it very quickly because that glass is fully down super fast if it moves too much you can actually cracked
go get some more glass in the same raw they go back to get some more color again these powder colors almost hit here instantly so I don't have to take a reheat for waste time with that it's very quickly get some color more
screen the stretch it out let me start to make the the hot glass and stick to other hot glass so these to adhere to each other I'll start to stretch it but I'll leave it short that way it's not falling back on itself it also helps it hold heat so I can start to stretch it out and then curl up a little step now the stem again is still very stretchy so I can turn into a handle and I have some time to shape it before it completely cools and sets up
why not pumpkin boat now if I look this cool down they will crack so while it's still hot you want to grab it and put it the kiln Zacks going to open for me here it's called an eel eel oven right now there's just holding it about 900 degrees so that it doesn't crack or break anything else it's also cold enough doesn't stick anything or losing shape then when we're done for the night that will pull down over about nine hours that's slow and even amount that nothing cracks there's no stress that way you end up with these beautiful things like this you
you
you
you
hi solar back door Zach and that special woman you can dish it out here like some pears and carnival stuff just a little bit yeah we actually have a studio in Cleveland Ohio of you two I pretty much introductory classes on there to our small groups about four people up for glass blowing a trooper lampworking we focused primarily on solid glass the first time but i always do offer a couple blown pieces of solid glass is definitely a lot easier to learn beginning together exactly it's kind of just like learning to ride a bike before you take the training basil kind of want to get a feel for it and you can move on to making it hollow I kind of start off with the furnace teaching how to gather you know teaching about you know physics the gravity of it you know not to be afraid of you know when their fall on the ground color times pretty much not going to you're going to make a mess the first couple times you do it it's expected it's a lot of fun
most the time I do like glass flowers I can get into a little bit yeah exactly I've been doing the pumpkin through fall rule solid glass ones all right we had two hours how much is the class but what we run group on right now and so the groupon is about I think it's about 50 before tax otherwise that I think it's about I think it's a hundred dollars before Jack so mostly we deal with a lot of groupon coming in expression for the intro the boy advanced classes are pretty much all cash or credit we don't really run
very more knowledge more money that's the general romance twice everybody out of my classes you the more advanced drawer the longer the classes going to be could be a little bit more money for that class because I have to set up for 78 days knowledge custom exactly yeah hey that's good that's good knowledge houseboat exactly okay so if anything is interested in taking your classes how we're going to get in touch with them oh well we have our website which is djm glass calm we also on facebook though I Oct glass facebook facebook will have city glass okay i'm trying to get instagram started right now it's just me and dan so we have all you know we're booked pretty far out right now so it's hard to keep everything running out or sure so like you said if you guys want to get in touch with an the links for their website and their facebook is going to be in the description below and it also put it in the video and stuff so so you guys can see it but like i said this has been ohio city glass you guys are interested in taking a glassblowing bosses definitely get in touch with these guys this has been we all right guys let's go away myers miss outdoors i hope you enjoyed this video if you did there's some more of my previous videos that are playing in the screens to my left right now there's also a subscribe button over there if you haven't done so i'll appreciate if you subscribe to the channel to stay up to date with what I'm doing with my school and the youtube channel estate posted on the videos that are going to be uploaded you can go to WWF ace be calm for / mass outdoors or you can go to ww mas outdoors LLC com like in my videos helps me and my channel out a lot I appreciate our reviews comments and support and hopefully we'll see out the woods
About the Author
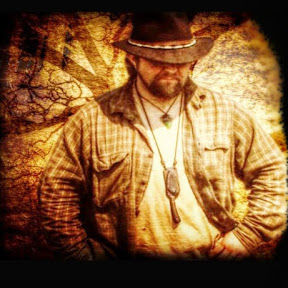
William Myers MantisOutdoors
Modern and primitive skills, fun in the woods and product reviews
More articles from this author
- How to build a Fire Kit and conserve your packable resources
- How To Build A Arapuca Bird Trap -Mantis Outdoors
- wild edible and medicinal plants 3
- Tribe Provisions Hammock and Bug Net -Mantis Outdoors
- Kelty Tioga 5500 Classic Backpack - Mantis Outdoors
- bow drill techniques
- mossberg 500 835 590 trigger assembly part 2
- Bob Dustrude Quick Buck Saw - Mantis Outdoors/Preparedmind101
- cold weather shelters Mantis Outdoors
- Pack Food -Mantis Outdoors
- I got lost in the woods part 1
- mossberg 500 835 590 trigger assembly part 1
- flint and steel fire
- Look for widow makers
- improvised sail needle compass
- Natural Tinders Fatwood
- Survival Trapping At The Waters Edge - Mantis Outdoors
- How To Safely use a Axe -Mantis Outdoors
- Water Decontamination Part 2
- The crook knife
- Wild edibles part 1
- TRAYER MULTI FLAME TOOL WINNER
- Building the get home bag
- LT Wright Genesis: Best Bushcraft Knife? - William Myers Mantis Outdoors
- How To Make Feather Sticks
- Debunking the Survival kit snare -Mantis Outdoors
- Mora Companion $5.00 to $20.00 range
- bird cage trap
- Tohil lighter
- Channel update
- wool blanket tricks
- LTWK Genesis Holiday Giveaway
- Foxtail hammock review and easy setup guide
- Barrel and Blade Box -Mantis Outdoors
- Trayer Fire Tool
- longhunter kit from nativesurvival
- fire piston
- mossberg 500 835 590 trigger assembly part 3
- E-cig fire
- Ferro rod techniques
- Winter weather clothes and the importance of WOOL!!!!
- Mantis Outdoors gear review: The Pathfinder Scout from bhk
- Mantis Outdoors SOSPES knife and kydex from Tortuga Hard Cases
- chaga:- some info on my favorite mushroom
- Natural Cordage
- 4H FOREST TO TABLE YOUTH AND ADULT OUTDOOR PREPAREDNESS
- Duluth Bushcrafter Pack Raffle
- How to build a pocket fishing kit -Mantis Outdoors
- Natural tinder: Grape Vine
- Merry Christmas
- Channel Trailer
- wild edibles part 2
- PRIMITIVE CONIBEAR (BODY GRIP) TRAP
- RICK LINDSEY FERRO RODS
- Safety pin mods and primitive fishing gorge - Mantis Outdoors
- Bark River mini Aurora review and GAW -MantisOutdoors
- Wild edibles and medicinal plants onion
- bow drill chaga
- primitive container part 1 of 2
- Hightower Custom Ferro Rods
- JX2 Jessmuk -Mantis Outdoors
- How To Build A Small Sewing Kit
- Survival Frog Fire Laces - Mantis Outdoors
- Releasing a non target raccoon
- burliegh balm
- Wild Ways Camp
- Rostertrucker flint and steel
- Roycroft pack frame
- How To Make natural buffing compound from a quartz rock
- Titanium Canteen Kit -Mantis Outdoors
- Making Bees Wax candles pt2
- The Trayer wilderness multi-flame tool and give away
- Knots You Should Know -Mantis Outdoors
- The Woodsmen from Hornet custom knives -Mantis Outdoors
- Foxelli MX500: Awesome $30 Rechargable Headlamp - Mantis Outdoors
- BEST SCOUT CARRY SHEATH VOYAGER LEATHER WORKS
- LTWK Overland machete - Mantis Outdoors
- Chaga tea and tincture in the home
- Pathfinder field bag winner
- Using A Net As A Pack
- Fish Tin Mods
- LUNCH TIME!!!!!
- One Tigris Mosquito Hammock (Budget Friendly)- Mantis Outdoors
- Poison Ivy & Jewel Weed
- 2015 edible plant class -Mantis Outdoors
- Knots
- Campingsurvival.com $300.00 monthly GAW -Mantisoutdoors
- Intro to CHAGA
- Camp Cookin' with Chef Will - Mantis Outdoors
- Jeff White Long Kephart Knife
- Bark River Aurora Mini GAW Winner
- Bees Wax Candles From Mantis Outdoors
- Wild edibles in the backyard
- Basic Woodscraft 101 The Tent Peg
- spring time 72hr load out
- Wraping up in a wool blanket
- P A C K ONE from Mule Team Canvas Company
- What I Carry On my Body In The Woods
- How to make bees wax candles that also fit the uco candle lantern
- How To Build A Hunting Kit
- Sure Fire Why Carry It?
- Building a Bow Drill set with a new student from start to finish
- How Knives Are Made At L.T. Wright Handcraft Knives Part 2
- Knife Safety
- Whats Your Grind -Mantis Outdoors
- What Food I Pack For 3 Days -Mantis Outdoors
- Voyager Leather Works Pouches
- Field sharpening kit -Mantis Outdoors
- Feather Stick Fire
- Hidden Woddsmen Bushpot Bag
- OUTXE 16,000mah Rugged Power Bank - Mantis Outdoors
- Natural Tinders -Mantis Outdoors
- Tree Identification 101 -Mantis Outdoors
- How to use duct tape for fire tinder
- Mess kit first aid
- gear list
- Duluth Bushcrafter Pack Raffle Winner
- Pathfinder field bag review and challenge sponsored by the hidden woodsmen
- Sharpening knifes and other tools
- Olight S1 Baton: Best Compact Flashlight for Outdoors? - Mantis Outdoors
- How to make a Birch Bark Container
- How to waterproof canvas
- Showing Connor animal stalking techniques
- How to navigate using the sun
- cayenne pepper first aid
- 2014 Pathfinder Gathering
- Old Hickory Butcher knife best $13 00 Knife money can buy
- Plants in your yard- Mantisoutdoors
- product review: UCO Candle Lantern plus L.E.D
- Boreal shirt from lester river bushcraft
- Wild Edibles and other Camp Cooking
- Habilis Bushtool Booth At The pathfinder Gathering
- Mantis Sospes G.A.W. -Mantis Outdoors
- Net Making Part 1
- Flexcut Carving Jack -Mantis Outdoors
- Zach trout from Tortuga hard case Kydex Wallets!
- Pyle Pdwm96 wireless lavalier mic
- collecting and rendering tallow
- Winter weather clothes part two
- Don Gamber leather hip pack
- Primitive Traps (FIGURE 4 DEADFALL)
- Hudson bay pack or Bed roll pack
- Common Mallow (Malva neglecta) Great Wild Edible
- Into The Woods 101 Mantis Outdoors
- Quick Cold Weather Shelter
- Identifying plants in the winter
- OLIGHT i3s best and brightest small light
- VERSATILITY OF THE TWITCH UP OR SPRING SNARE
- Fire Challenge -Mantis Outdoors
- Survival Filter Pro -Mantis Outdoors
- Primal gear unlimited take down bow
- Net Making with a Net Needle and a Net Gauge -Mantis Outdoors
- Squirrel Pole/Spanish Windlass Primitive Trap - Mantis Outdoors
- Survival filter review - Mantis Outdoors
- REVIEW ON THE The Pathfinder Tarp / Poncho
- Flat Figure 4 - Mantis Outdoors
- Water collection and decontamination
- LT WRIGHT HC BUSHCRAFTER GAUNLET REVIEW PT1 -MANTIS OUTDOORS
- Thrunite TH20 Long Term Use Review - Mantis Outdoors
- How Kydex Sheaths are Made With Copperhead Outdoors -Mantis Outdoors
- L T Wright Kydex -Mantis Outdoors
- (The Gauntlet) Dogwood Heritage Echo-7 Part 2 - Mantis Outdoors
- Hidden Woodsmen Haversack -Mantis Outdoors
- ALS AND SUICIDE PERVENTION CHALLENGE
- Fatwood and ferro rod techniques
- Improvised Fishing Pole -Mantis Outdoors
- How Knives Are Made At L.T. Wright Handcraft Knives
- My Most Used Headlamp (After Months Of Use) - Thrunite TH10
- Emergency Prepping For Hunting Season - Mantis Outdoors
- Fresh water from a spring no treatment needed
- Budget blade $50 to $75 range: Condor Crotalus
- natural tinders- birch bark
- Autumn Olive
- Answering Some Questions about Birch Bark
- Condor Huron (Navajo Knife) First Impressions - Mantis Outdoors
- Wilderness Loom and Grass Mat Weaving -Mantis Outdoors
- Net Making Tools -Mantis Outdoors
- HOW TO BUILD A HAVERSACK KIT
- I got lost in the woods part 2
- Titan Survial paracord -Mantis Outdoors
- Primitive Torch
- Dark Timber Bushcrafter by Peter Kohler
- Making A Four Tine Fish/Frog Spear w/ Bobbi - Mantis Outdoors
- Micro Inferno Torture Test
- Wild parsnip
- Tarp Hack, Tips and Tricks -Mantis Outdoors
- spring snare made easy
- Bark River 3V Bushcrafter - Mantis Outdoors
- I Got Lost In The Woods Part 3 - Mantis Outdoors
- Weather wool clothing -Mantis Outdoors
- NOMADIK SUBSCRIPTION BOX -MANTIS OUTDOORS
- Old Timer Carving Knife Vs Flexcut Carving Jack - Mantis Outdoors
- Win A Green Elephant Ceramic Rod! - Mantis Outdoors
- Freehand Sharpening Part 1-The Beginning - Mantis Outdoors
- Camp cooking
- Pack Cooking Kits -Mantis Outdoors
- Power in the Woods -Mantis Outdoors
- Thrive Freeze Dried Food -Mantis Outdoors
- Camp Breakfast with Thrive Life -Mantis Outdoors
- Uco Sweetfire Showdown -Mantis Outdoors
- Primitive fire from start to finish -Mantis Outdoors
- Foxelli Solar Panels -Mantis Outdoors
- Turkey Tail Mushroom -Mantis Outdoors
- Olight M2r Warrior -Mantis Outdoors
- NXN (northxnorth) Merino Wool -Mantis Outdoors
- MANTIS OUTDOORS APPAREL
- The Huntsmen from Quickhatch -Mantis Outdoors
- ESBIT COOKSET AND ALCOHOL STOVE -Mantis Outdoors
- LTWK Patriot knife -Mantis Outdoors
- Fox River EXT1 From Bark River -Mantis Outdoors
- Ben Orford Sloyd Carver -Mantis Outdoors
- Bark River Mini Bushcrafter -Mantis Outdoors
- Camp Dinner With The Ndur Cookset -Mantis Outdoors