How to make a Boot Rack from reclaimed Wood - TA Outdoors
Description
Graeme is back in the garage with another diy video! This time he uses some reclaimed pallet wood to make a Welly boot rack for free! It's a very simple but practical design. The boot rack helps to dry out your Welly boots. He finishes it off with some varnish to make the final product a little more durable. If you enjoyed the video feel free to subscribe for more.
TOTALLY AWESOME OUTDOORS
-----------------------------------------------------------------------------------------------------------
Click here for more PALLET WOOD videos: https://www.youtube.com/playlist?list=PLxnadpeGdTxBSvWfEXz2B5y9hEcMLGhVd
-----------------------------------------------------------------------------------------------------------
-----------------------------------SOCIAL MEDIA-----------------------------------------------
Facebook ? https://www.facebook.com/totallyawesomeoutdoors
-----------------------------------------------------------------------------------------------------------
Check out our other YouTube Channel:
TOTALLY AWESOME FISHING:
https://www.youtube.com/user/TAFishing
If you wish to send me stuff:
Mike Pullen
PO Box 7466
HOOK
RG27 7NA
Tags: How-to (Website Category),Do It Yourself (Hobby),Hobby (Interest),make your own,diy,free,pallet wood,welly boot,boot,rack,boot rack,simple,cheap,wood,varnish,practical,quick,tip,tips,ta outdoors,totally awesome outdoors,graeme pullen,graham pullen,mike pullen,outdoors,wilderness,save money
Video Transcription
welcome to the totally awesome outdoor show now I was going outdoors honestly to do a bit of garlic some pre-cut and usual sort of stuff that we get here and the winter fall I'll put the wedding since on ah dis Casti i'll be i'll have it let them out the rain are not completely stupid but they've been a help they got dead they drew on the moisture in there and there's nothing worse than putting a wet wedding on what you should do is make yourself a wedding crying Rack is really a wedding back upside down and if you put them upside down like this obviously not that way around that way when the air can circulate the moisture comes out they dry out and they be nice and cozy when you put them on how would you make them hmm or a compelling would ya you knew I'd say that didn't you but little bit of a business here because I'm not varnishes well this little paint in it I using some of the struts the go across rows across the palate board and this is a call it slightly better quality one and it's been planed it's not ruffled it's plain wood so that's lucky for me there cross-section I mean this is so easy as ridiculous cross-section standard pallet wood I'm going to run the sanding and belt sander over that one but to make the poles I could use something like broom handle something like brake handle any piece of a third wouldn't handle but i'd rather sell some because i love things for nothing in my store i had a couple of brand-new badass the rails you know that go up the stairs a couple of used ones because i've already notched a little got angles on them and ok so there's slightly different patterns just they're turning points but i feel it's better than just a straight route it's a little bit of shape i'm going to cut them across the middle and measure them obviously cover you want them to let me just show you this one what the length of the word to which is generally i think around about 18 inches the average well if the boot could be any boot in fact that not to be well if there's any boots will dry so allow there and allow a little bit of space sayre hall isn't that convenient it comes up where that little pretty notches so I figured if I cut either side of that notch it should be hopefully he says or you won't be look at that equidistant and that will clear the base their wonder the tip is i would use rather than jigsaw I'd use a ten and so on because it's a finer tooth cut there obviously we jigsaws you can buy different blades for them but because it's such a wide actual support blade there when you're sawing straight nice and smooth it won't sort of Kent off at an angle like this and twist and go off when you get a cut as or peculiar so I'm going to cut dead straight there dead straight here and obviously these two ends are flat yeah those are just nip off make sure they all the same measurement so just for neatness right I go on these cutter or the spindles the balance of pins now's the time to get some coarse sandpaper just take the edges of them you know we've got the rough saw cut because if they're going upside down and your boots going to arrest on them you don't to get split or anything like that to you the other thing is if you are going to strain it down to time just to clean up getting the finger marks and serves up there and then the varnish it take for the stain would make a bit better ok I'm going to use a piece of this timber this is so easy to dickless you do want to use is too heavy bass pieces because you don't move away to the boots tipping over also if you're going to have them hanging like this just just just make sure you've got enough for in my case here one two three pairs of boots afraid the dog is going to have to go without have down Wellington's I'm going to put these two pieces of touching just to make my base and a little piece of sawing off pallet wood neat piece not with the nails across the top there just like that to lock those together to give you my base and then I'm going to drill long screws right the way through and into the base of that spin book so no exactly rocket science but I'm again going to cut this with the tenants or I don't know whether people realize this but if you haven't got an angle straight edge here another guy is just a quickness if you lay a saw here you've got a right angle generally between the molding here the shaft during it to the handle and as long as you get it straight and flush there let's see the pinched up tight you can actually cheat and use the saw itself to give you a straight edge if you want to check if this one straight you can measure there and you generally will find out with a modern saw that hasn't been used a lot that will stay at 90 degrees and don't forget this blade is actually molded in there there's no screws to rock loose so if it were screws this could rock and change the angle from 90 degrees it could be 80 it could be 110 it could be either way there won't be the right angle but because that's molded in there that should be 90 degrees there as you can see perfect and then a way I'll go cutting just align your thumb against the side of the blade here and the don't just Ram it forwards the best way to start a cut is to draw backwards which is the reverse of the way the teeth cut just like that then you put a little notch which you can start pushing it and you can keep your hand away you can guide it I tend to keep my hand away get it look like this obviously make sure the blade doesn't hit this to work do not go mad and do not force it the saw has the teeth the teeth will do the cutting for you you just have to keep a mild pressure on it keep it dead straight and it should pretty well cut itself with one cut itself Graham talk sense just trying to make it easier for you now a 10 and saw cuts traitor if you tip the blade back that way it's more for shallow good like this that way the blade is cutting through a lot lot shallower it's not the deep woods always finish your last goes off slowly cop nice clean edge I've got my base boards there I've cut my support place we're going to join them together here both sides on each end where the same on that in now if you want to clean something up just as a tip here get are you using sandpaper smoothness here to show you and you want to clean out the wood so nice varnish finish on it generally most people bigger piece of sandpaper up like this and away we go like just working away working away working away when you tend to get ridges like that because you're only using one pressure point or your finger with your thumb if you get one of those off cuts of pellet would tuck the block the little wood block like this it's nice and flat and even and that way huh not only do you not get splinters you get a nice clean finish to the wood and it will make it even providing the wood block probably even to start with now it's time to clean up still be screw together okay line up your two in blocks here nice and neat and then I put my little support where mine this piece of wood you would think our how's he going to screw it's going to make an asymmetric shape here with one spindle coming off in one off him no this is going to be the feet that it stands on I'm actually going to fick fix through there and the top is going to be the other side but what I want to do is drill a pilot hole here first just through
power just want to go through that top piece of pallet wood now you could counter sink this otherwise the screw might make it rock but generally pallet wood is quite soft so I'm just going to fire a couple of screws in just enough to nip into the wood and if you over set the talk set in Maori you would have a talk setting here to stop you burying the screw I want to bury it so Chuck's are going to come in slightly off the maximum all we've come a power and it should there's are not there so i might not be able to bury in the north that's it that's buried if i had the talk setting on like this you can feel that still sticking up so i just increase the torque setting sit i bite that screw just a tad more that's it don't do it too much because it will spin and tear out the wood same at the other end two feet done ok so I'm drilling six pilot holes in the center of this back piece of tinder we go right through if that doesn't go completely flu and you never little drill long enough I don't want to go to a bigger drill I just put the bit drill bit in the Chuck and extend it my little bit of done physically huh I wonder how many times I've gone through the workbench it has happened doubtless will happen again okay I've got my screws and I'm going to make these as you can see they're quite a thin screwed don't want a fat one the reason being it's got a flight up into here if I go to fat it's going to split obviously gonna put some grid glue around them as well and we're going to pilot drill this hole here so that's the first stage of they'll do but just check for your screw height this is obviously upside down is going to the screw will go through that way but just for the purpose of showing you this you can imagine it's there so with some glue I got about an inch and a bit of support as well bear in mind is only taking and Wellington boot weight and vertically at that the next stage is to drill out a pilot hole down the end of here a very small drill because you've got to still leave some wood for the screw thread to bite on if you use to bigger a drill bit it's just going to be loose in there so you wanted to be tight and I'm probably get a pre drill it about half a length of the screw that I've got left best done in a vise I feel because you can keep everything nice and square you
okay so let's got all the holes drilled the little pilot holes now here's a little tip put these over one side you'd be tempted to use that that beam there and put the supports right in the middle I think that's about right but when you look at the boots because you wanted to hang straight if you put the actual support there and the back heel of it it kicks over like this is kicking over and he's pulling like this so when you slide your boot on you want to put it at the front see it balances like this it balances and supports here rather than a heel if you put it the heel it kicks forward is straining those screws and the glue if you if you put your boo there so what I'm saying is you need to allow for that and therefore bring that support block forwards a bit because you might want to put this against a wall or support so put it at the front there and that gives you a couple of inches or so in the back spare look it's not rocket science you can move it around it's like all common sense and we're going to do I'm going to trip grill out these holes here there's slightly bigger drill going right through here but I'm going to need an extra longer screw here because I'm going to have to go through the feet there's pizza port as well that way the grill goes clean through the base plate but actually bite into this piece of course i'm going to put some glue in there as well any March you get like this with pencil marks just take them out using the block and sander that way when you come to varnish will stain it it's all true serve on this is yo Bernice no it's never going to be seen any way but I like to work do things properly or any chance the spindles don't line up vertically get yourself a spare piece of pedal would write this and all you could do is with a cleaver or knife just balance it shave off a couple of very thin strips soon as you can get more your fingers on using it cleaver these can be used as balancing wedges to level it up I'll show you in a second taper the ends with a Stanley knife or what I call a box cutter and then you can push it dead vertical and the glue should set with that underneath it that's if you have grilled any angles or holes into those spindles incorrectly now if you have to drill any holes slightly off vertical and it does happen I just don't want purposely just to show you this this is a tip for anything that you have to get out of a sticky situation is if you get a block just shave a few bits down on the cleaver with a knife or something like that no knots in the wood it needs to be a straight grain run it down you can rock the knife like this shave off a couple of pieces and you can use these as wedges get yourself a Stanley knife or a box cutter just cut off the surplus here just to give you a little bit of a taper that's all you're looking for to level something up I've used as many times just for getting me out of trouble when I've done a big screw-up screw up I'm using screws but when I screwed up with something it is slightly out of kilter I'll show you how to get out of trouble especially when you do you know you're dealing with verticals because at the end of the day you still want to get it as low level as you can always be careful with box cutters
now you see how this one slightly over all you got to do here let me show you just briefly is slacking that screw off on that one just a tad that's all it takes yeah you see the anger you could have made the saw cut crooked only affect bass-heavy you could have drilled look if you want to pull it back to there ok so what you can do is you could ride one of these wedges under there just tap it under with a hammer by this year's pulled it back up level yeah so what you do is you put your glue on you get yourself all leveled up you having a wedge over you can either use a fine hacksaw you can move I just going to show you this bit thick edge of the 10 on just the tunnel day to telling the shortcuts on standards would ever need and that should look at that perfect absolutely perfect you'll see you cannot see that wedge just under here all I then need to do put it inside this is obviously when the glue sir give it a tweak with a gun and that is not only rigid but its vertical as well double check it first while the glue still wet as you can see I just show you the different say if you put the book on the heel see her tips forward and it's straining the spindle that way so when you put it down put it at the front end slide it down and there your balance it hangs perfectly in the middle let's get these glued up we are giving well on the way right so I'll getting them all lined up I've got my wedges going to use a piece of wedge and I've got the pip of the Scrooge's there I'm going to put some wood glue wood adhesive on there as well so it's got sort of double brother if the glasses out see what's are pouring out now you can do it with the nozzle where you can do it I can't do it it now tell you what I'll do it now because I forgot to put a pin or a nail in the end of this or a cap so it's don't cut it up inside we've all been there with all make mistakes just put a little bit on the top there locate your spindle like this as you can see and then just tighten up with or without a way to adjust it accordingly I'd suggest doing each one in turn I've always going to get glue everywhere okay call the spindles tightened up there but you might want two extra tight the music a good short fat dumpy hand grip one because you could generally get more pressure on that and of course you can twist the spindle back so what are these are slackin the spindle off I tighten the screw as far as I can and then I bring the spindle back to the level with a bit of a twist so slacking it off a turtle to cool the turn on tape as I can get and then I've got an extra bit of up there but going to rotate that spindle itself onto the screw this one put the screw into the spin of them tiny up yeah just tight as I can just to give me that extra bit of fight and then we got to do hey you might also have noticed every here that's tight I've countess up here to the depth of this would they are counter something that extra thickness to allow the top so that when i get the tops they're all pretty well level i got some 21 paris business here I'll call them kid sized ones these are add up and at all that's what I've allowed for you do now just wipe off that surface blue sure they're all straight let that set and then my final was over with the sandpaper clean up and I think you know I think we're going to give these a nice bit of vons because they're going to be in a port for they're going to be outside anyway you want to look halfway decent now that would be the next phase okay final tip is when you're doing staining over new would try and finish in the direct 10 don't try you must finish in the direction the grains running don't do it crossways because as you can see you just get residual bits from the paint there they're drying the hall for so try and get with the with the flow the values and with these spindles anything that's like this with round edges just go over them lightly just before you think you finish when you think you've finished trust me you haven't uses a bit there I've missed just try and finish in a nice even stroke lightly with the brush and check for any runs and we're nearly ready to let this dry come back and hang some boots on now there you have it put a bit on the top as well up here make sure that you put a good dollop up there because you might get moisture out the boots and that's an area that turn it could penetrate the wood now listen you can still make this our panel you don't have to use Spindler's I've only use these because they were free I had them left over you can use what you want pieces of wooden square inch by inch pieces of power cut in half you can use what you want it's a busa Paul I'll just use these so it's basically whatever you want to put on there put on there as long as you can get those boots upside down so the air gets to them that's all done let's let that dry and see what the finished product looks like I should be in the Tate Gallery so there you go all finished all dried off and you just put your boots on just rest them balance from there plenty of space I can get on there at least three pairs and even if using your size for the wife all for this all done everything's nice and dry when you take them off next time you will not hopefully add damp wet annoying feet thanks for watching a totally awesome outdoor show I'm sure there's going to be something else I can break Eric pallet wood
About the Author
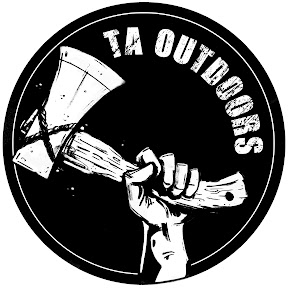
TA Outdoors
Bushcraft, Wild Camping, Wilderness Hiking Trips, Solo Overnight Camps, Shooting, Hunting and Backpacking. My dog joins me on some of the trips. His name is Jaxx.
My name is Mike. And I'm addicted to adventure...
Check out our other YouTube Channel TAFishing: https://www.youtube.com/user/TAFishing
More articles from this author
- Dorset Steam Fair 2016 | TAOutdoors
- Make a Pallet Wood Trash Can screen CHEAP & EASY | TA Outdoors
- Bushcraft & Fishing - Catch and Cook Deep Fried Fish on the Fire at The Bushcraft Camp
- Bushcraft Camp Update 11 - Hunting Tower, Dog House, Gate and Raised Camp Bed
- DIY TIPS - How to repair cracks in walls | TAOutdoors
- Making Bushcraft Chairs at the Shelter - Axe, Fire and Cooking too!
- Swedish Firetorch Cooking at the Bushcraft Camp
- Solo Overnight at the Bushcraft Camp - Fire, Cooking, Axe Work
- Bushcraft & Fishing - Catch N' Cook on the Camp Fire!
- NEW BUSHCRAFT CAMP!! + Tinder Fungus Fire
- Stoat Kills Rabbit on Camera! | TAOutdoors
- Cooking Pheasant at the Bushcraft Camp- Axe, Hunting Knife, Fire and Preparing Game in the Field
- How to Pluck and Gut a Pheasant | TA Outdoors
- 4 DAY MOUNTAIN ADVENTURE! [TRAILER]
- Bushcraft Camp with my Dog - Wall Weaving, Campfire and Cooking Bacon on the Grill
- How to TRAP & KILL RODENTS | TA Outdoors
- Bushcraft Cookset - Crusader MK2 Review & Test | TA Outdoors
- Beachcraft - Survival on the Beach | TAOutdoors
- 3 Days Alone in the Wilderness - Fishing, Bushcraft & Foraging for Wild Food
- How to Track and Stalk wild Deer | TA Outdoors
- BUSHCRAFT & SURVIVAL CHALLENGE!! - Lighting a Fire with ONE HAND ONLY!
- Bushcraft Camp - Roof Pulley System for the Shelter + Fire Pit Cooking
- Making a Wine Rack from Free Pallet Wood, Cheap and Easy! | TA Outdoors
- Alcohol Stove Review | TA Outdoors
- Amazing fish recipe! Rainbow Trout Curry | TA Outdoors
- Sami-Style Oilskin Pouches for Bushcraft | TAOutdoors
- Bushcraft & Survival - Catch, Kill and Cooking Fish at Camp
- Bushcraft - New Knife, Flint & Steel Fire + Cooking at the Camp
- Emergency Survival Fire Starter - Char Cloth | TA Outdoors
- How to lace up a Hiking boot - Simple and Easy! | TA Outdoors
- Tree Root Survival Shelter - Fast Build, Minimal Tools
- Bushcraft, Hiking & Camping Backpacks - Which one is best for your needs?
- Bird Hunting - Shooting Pheasants | TA Outdoors
- Hunting with Ferrets | TAOutdoors
- How to make Natural Cordage from Tree Roots | TAOutdoors
- Bushcraft - Camp Fire with Pot Hanger, Coffee and Day Pack Gear Overview
- Solo Camping under a Tree Root - Stone Fire, Raised Bed, Cooking Tripod
- How to make a Bookshelf from Pallet Wood for FREE! | TA Outdoors
- Bushcraft Gear Hanger | TAOutdoors
- Bushcraft Fireside Camp Chat - Episode 1 | TAOutdoors
- Preparing My FORT for Winter - WINTER IS COMING!
- Foraging for Wild Food with my Dog | TAOutdoors
- Bushcraft, Camping & Hiking Tips | SHED SUNDAY EP. 4
- The Ultimate SURVIVAL TOOL - This thing is a BEAST!
- How to fix a bilge pump for boats | TA Outdoors
- Walking in the English Countryside | TA Outdoors
- Bushcraft Camp Update 5 - Secondary Shelter! | TAOutdoors
- Solo Overnight Camping - Tipi Tarp Shelter, Campfire, Grill Cooking, Knife work
- Bushcraft Camp Update 1 - Bushcraft Breakfast | TA Outdoors
- Introduction to Air Rifle Shooting | TAOutdoors
- Bushcraft - Winter Camp Fire Cooking in the Shelter
- How to skin a Rabbit | TA Outdoors
- Hunting Tower, Campfire & Stalking Deer with HD Cameras at The Bushcraft Camp
- How to cook fish - Awesome Curry Cod | TA Outdoors
- Beach Fishing and BACON!
- 12 Wild Camping Tips - How To Do Your First Solo Wild Camp | SHED SUNDAY EP. 1
- Making a Christmas Wreath from Natural Materials found in the Woods
- Bushcraft - Making a Fire Reflector the easy way | TA Outdoors
- Awesome water bottle tip! | TA Outdoors
- Camp Cooking at the Bushcraft Shelter on the Fire Pit and Grill
- 5 Tarp Shelter Setups for Bushcraft and Camping in the Woods
- Coastal Safety by The Coastal Survival School | TAOutdoors
- Beach Fishing and Cooking Fish over a Fire | TA Outdoors
- Solo Overnight at The Bushcraft Camp - Minimal Gear, Lightweight Campout
- Shotgun Shooting for Beginners | TA Outdoors
- Bushcraft Camp Update 2 - Log Seat Build | TA Outdoors
- Bushcraft Camp Update 3 - Improving Shelter | TA Outdoors
- How to Light a Campfire with Natural Materials and a Ferro Rod
- Bushcraft Camp Update 7 - Cooking Set-up | TAOutdoors
- Hiking in the Rain with my Dog - Warm Fire, Knife Work and Coffee at The Bushcraft Camp
- How to attract wild birds to your garden | TA Outdoors
- Bushcraft Camp Update 6 - THE FIRE PIT!! | TA Outdoors
- Easy to make Boot Remover | TAOutdoors
- Making a Leather Tinder Pouch by Hand
- How to make a Recycled Pallet Wood Coat Hanger & Mirror | TA Outdoors
- I Need To Get This Off My Chest...
- One Stick Fire CHALLENGE - Boiling Water with ONE STICK ONLY!
- Bushcraft Camp Update 4 - Perimeter Walls Finished! | TA Outdoors
- Bushcraft Shelters - Tree Root Shelter with no tools | TA Outdoors
- Make a Boat Bookshelf from Pallet Wood | TA Outdoors
- BUSHCRAFT: Den Building Diaries Part 1 - Natural Shelter | TA Outdoors
- Bushcraft Portable Sawing Horse, Table and Log Collecting Tips | TA Outdoors
- Bushcraft - Using an Ancient Saw on Logs + Cooking on the Fire at Camp
- How to cut wood | TA Outdoors
- How to make a Picket Gate from Pallet Wood | TAOutdoors
- 4 Day Solo Wild Camping Adventure in the Mountains
- Awesome Lamb Race!! | TAOutdoors
- Shooting - The Shooter's Stew | TA Outdoors
- Bushcraft Camp 2 - Wood Cooking Tripod, Latrine, Axe, Knife & Cooking on the Campfire
- Bushcraft & Fishing - Catch and Cook Fresh Fish on the Grill at The Bushcraft Camp
- Coastal Foraging For Beginners - LATE SUMMER | TAOutdoors
- Survival Tips - How to Kill, Fillet and Cook Fish | TAFishing
- Primitive Shark-Tooth Knife! Gutting and Preparing Fish at the Bushcraft Camp
- Fishing & Bushcraft - Catch, Cook, Fillet and Solo Overnight Wild Camping in the Forest
- One Man Tent Review - Yellowstone Matterhorn | TA Outdoors
- Taking my Dog and my Girlfriend to The Bushcraft Camp + Subscriber Gifts!
- Fishing: Catch n Cook in a CAVE & CAVE EXPLORING!
- Making a Mood Lamp from reclaimed Pallet Wood | TA Outdoors
- New Bushcraft Campsite Permission!
- Fishing & Bushcraft - Catch, Kill & Cook on a Campfire
- Making a Bushcraft Chopping Log | TA Outdoors
- DIY Survival Container from Recycled Bottle Caps! | TA Outdoors
- Solo Camping in the Forest - Fire Reflector, Tarp, Camp Fire, Axe and Knife Work
- Bushcraft Camp Update 10 - Natural Shelter expansion, Camp Construction, Axe, Knife & Saw work
- My Top 3 Fishing Knots - Strong, Reliable and ones that YOU NEED TO KNOW | SHED SUNDAY EP. 2
- New Bushcraft Camp Construction - Site Clearing, Firepit & Bacon Breakfast
- How to clean a Shotgun | TA Outdoors
- NO WAY! My Dad has taken over my Bushcraft Camp!!
- Overnight Hammock Camping in the Woods - Camp Fire, Tarp, Knife and Camp Tips
- Bushcraft Burden Strap | TA Outdoors
- Solo Bushcraft Camp in a Bug Infested Forest - Giant Ants, Spiders and Mosquito
- Axe Madness! Using 7 different Axes & Hatchets in the Woods + Camp Fire Cooking
- How to use a Woodburning Stove | TA Outdoors
- Wilderness Gathering 2016 | TAOutdoors
- Shooting Targets from The Hunting Tower at The Bushcraft Camp
- How to service an oil lamp | TA Outdoors
- Bushcraft Backpack Review - Snugpak Stamina | TAOutdoors
- Epic Camping & Survival Gear Giveaway!
- Shooting - Scoping a Deer Rifle | TAOutdoors
- Bushcraft Fire Lighting: Birch Bark Fire | TA Outdoors
- The Dangers of Shotgun Shooting at Close Range | TA Outdoors
- How to cook fish - Pan fried and baked Whiting | TA Outdoors
- Bushcraft Camp Update 9 - FIRE, SHELTER, COOKING & LOG STORE!!
- Epic Airgun Range!! | TAOutdoors
- Pike on a Bike! - Pike fishing tips | TAOutdoors Show
- 3 Day Camping Trip with my new Puppy! | TAOutdoors
- Day Camp - Hammock, Tarp and Chill in the Woods!
- How to Upholster a Chair -Simple and Easy! | TAOutdoors
- Hunting Dogs - Working The Woodland | TA Outdoors
- Bushcraft Camp Update 8 - Raised Camp Bed | TAOutdoors
- How to make Survival Fire with natural oil | TA Outdoors
- How to make a Plant Pot Stand from Pallet Wood | TAOutdoors
- How to build a FREE Garden Table from recycled pallet wood | TA Outdoors
- Bushcraft Knife Review - TBS Boar | TA Outdoors
- Clay Shooting at Bisley - Behind the Scenes of the Traps!
- 10 Knots for Bushcraft & Camping - How To Tie Knots | SHED SUNDAY EP. 3
- Bahco Laplander Folding Saw Review and Test | TA Outdoors
- Shotgun Silencer | TA Outdoors
- Bushcraft Shelters - The A Frame Shelter | TA Outdoors
- How to build a LOG STORE with PALLET WOOD! Cheap, Simple & Easy! | TA Outdoors
- Bushcraft Camp Shelter - Campfire, Long Hike with my Dog, Folding Wood Stove
- Catch n Cook - Spit Roast TIGER TROUT at The Bushcraft Camp
- Cooking Steak on the Grill at The Bushcraft Camp - Log Cabin Fire, Wood Splitting.
- Overnight Solo Camp in a Canvas Tent - Bushcraft, Axe Work & Campfire
- Bushcraft & Fishing - Catch and Cook Smoked Fish at the Log Fort Camp
- Bushcraft Camp Update 12 - Wood Roof Kitchen, Overnight Camp & Perimeter Wall Expansion
- Bushcraft & Fishing - Catch and Cook Pan Fried Fish on the Fire at The Bushcraft Camp
- Cooking on a Campfire in the Forest with my Dog.
- My First Aid Kit for Bushcraft, Fishing & Wild Camping
- Winter Camping in a Hobbit Tent and a Woodstove
- Building a Bushcraft Camp in the Forest - Wood Saw Horse, Tarp Chair, Log Cabin Notches
- Shooting with Shotguns and Air Rifles - Forest & Field
- Building an Off Grid Cabin in the Forest using Free Pallet Wood - A Wilderness Project
- Winter Hot Tenting Alone in the Forest with a Canvas Tent and a Woodstove
- Off Grid Pallet Wood Cabin Build in the Forest for Free - Wood Floor, Wall & Frame Structure
- Log Cabin Life: First Night in the Off Grid Pallet Wood Cabin
- One-Man Off Grid Cabin using Free Recycled Pallet Wood - Roof & Front Porch Build
- Log Cabin Life: Alone with my Dog in the Off Grid Pallet Wood Cabin
- Building an Imperfect Cabin in the Wilderness for Free - Recycled Pallet Wood Project
- Bushcraft ft. ALEC STEELE - Fire Lighting, Steak, Axe work - Epic Day at The Camp!
- Off Grid Cabin in the Forest using Recycled Pallet Wood - Woodstove Cooking & Log Store
- Cabin Life: Snow at the Off Grid Pallet Wood Cabin - Unboxing Mail
- Bushcraft Camp Update 13 - Primitive Shelter, Fire Pit Cooking, Overnight Camp
- Primitive Survival Shelter Build with Bare Hands - No Tools Needed
- Recycled Pallet Wood Cabin Build: An Off Grid Wilderness Project
- Off Grid Tiny Cabin: Pallet Wood Projects & Cast Iron Grill Cooking
- Building an Off Grid Cabin for Free to Save Money - Woodstove & Pallet Wood Bed
- Coastal Trip - Wild Plants, Bushcraft, Scouting for Fishing Marks & Channel Update
- Off Grid Log Cabin: Recycled Pallet Wood Project - Roof Extension & Sink
- Bushcraft Camp in the Snow - Fire, Shelter, Axe, Cooking Fish
- Bushcraft Camp: Full Super Shelter Build from Start to Finish.
- 3 Day Solo Winter Snow Camp - Bushcraft, Canvas Tent, Woodstove, Bowdrill
- Off Grid Pallet Wood Cabin: Opening Subscriber Gifts & Coffee Vibes
- Primitive Fishing with Horse Hair and a Bamboo Rod - Catching Fish with a Stick
- Off Grid Pallet Wood Cabin: Picket Fence Build & Woodstove Cooking
- My Dog's First Time in The Snow + Truck Update - New Mods
- Bushcraft & Blacksmithing: How To Make a Bushcraft Knife with ALEC STEELE
- Cabin Life: Unboxing Fan Mail in the Cabin with my Dog (Incredible Gifts!)
- Forging with ALEC STEELE: Hammer Technique, How To Forge for the First Time
- Cooking at The Bushcraft Camp - Axe, Fire, Shelter, Wilderness Survival Tips & Grilled Kebabs
- CATCH and COOK: FRESH TROUT on the Woodstove at The Off Grid Pallet Cabin
- Making a Hatchet with ALEC STEELE - Forging with a Sledge Hammer!
- Solo Overnight Camp - Stealth Tarp, Winter Camping in Cold Rain, 100 Year Old Tools.
- Build a Bushcraft Dog House in the Forest Camp - Part 2
- 2 Days Camping Alone in a Tent on a Clifftop - Fishing, Hiking & Filming
- First Night Camping on the Roof of my Truck
- Building an Off Grid Cabin using Free Pallet Wood: A Wilderness Project
- Solo Overnight Camp in the Mountains (Truck Camping) - Lake District Adventure | Ep.2
- Pallet Wood Cabin in the Woods: Raised Vegetable Bed for Spring Garden at The Off Grid Cabin
- Camping in a River Valley - The Rain is HERE! | Ep 3
- Bushcraft Camp Update 14 - Tunnel, Fire Pit Upgrade, Blacksmithing, Wood Mallet Carving
- Taking my Wife and Dog to The Bushcraft Camp - Merch Release
- Bushcraft Camp - Solo Overnight in the Super Shelter, Axe, Campfire, Lean to Shelter
- How to Prepare a Deer for Food | Survival Skills | Bushcraft | Wild Meat | Wilderness Living
- Solo Overnight Hammock Camping - Bushcraft, Foraging for Wild Food to Eat
- Pallet Wood Cabin in the Woods - The Last Unboxing Video
- Primitive Log Cabin in the Woods - Moss Roof | Overnight Camp
- Bushcraft Camp with My Dog - Slingshot, Axe, Knife, Bowdrill Fire, Hunting Tower
- Overnight Bushcraft Trip - Camping in a Debris Shelter - Cooking Wild Meat on Open Fire
- Fishing for GIANT CATFISH - New UK PB!
- Bushcraft Skills - Axe & Knife Skills, Camp Setup, Fire (Overnight Camping)
- 3 Days Learning Bushcraft & Survival Skills
- BUSHCRAFT CAMP in the FOREST - Making PRIMITIVE GLUE, Repairing the SHELTER
- 4 Day Camping Trip in the Mountains - Lake District Wild Camping Adventure | Ep 1
- Building a Dog House Shelter at the Bushcraft Camp (Part 1)
- Catch n Cook with FREE HOMEMADE CHARCOAL| Pan Fried Fish - FRESH CATCH!
- Bushcraft Camp Update 15 - Wood Frame Roof Build (Super Shelter)
- Gorilla Tape Shelter Build With My Dog | Survival Challenge | Bushcraft Camp
- Catch and Cook BIG TROUT {GRAPHIC} GUT, CLEAN & FILLET | Cook on a STICK
- Bushcraft Day Camp in the Woods with a Canvas Poncho Tent
- Bushcraft & Fishing - Catch and Cook, Fillet, Clean Fish at The Bushcraft Shelter
- Solo Camping 24hrs Alone Overnight on the Coast - A Solo Adventure
- Build a Tiki Bar from Recycled Pallet Wood - Off Grid Project
- Leatherwork for Beginners - Basic Skills (Tutorial)
- Off Grid Cabin - Building a Free Pallet Wood Outhouse in the Woods
- Off Grid Cabin in the Forest - Roast Chestnuts, Woodstove (Camp in the Woods)
- Bushcraft Camp - Destroying Structures ready for Wood Roof Shelter Build
- Cave Camping: Cooking Snails, Fish, Wild Plants, Fire (Survival)
- Camping in the Woods like ROBIN HOOD - Military Poncho Tent
- Her First Time at the Cabin: Woodstove Cooking (Off Grid Pallet Wood Cabin)
- Bushcraft & Fishing - How To GUT & CLEAN FISH | BUSHCRAFT BOWDRILL FIRE | BAKED FISH
- Make a Leather Tinder Pouch | Bushcraft Kit (Tutorial)
- Off Grid Pallet Wood Homestead Build - Pallet Wood Projects at The Cabin
- 2 Day Bushcraft Camp with a Dog - Deer Hide Beds, Camp Fire Cooking (Forest Camping)
- Bushcraft Camp Update 16 - Thermal Shelter Upgrade (Survival)
- Make a Survival Zip Pull from Paracord (Tutorial)
- 3 Day Camp in the Woods - Bushcraft Shelter, Dog, Wool Blanket (STORM FORCE WINDS)
- Solo Bushcraft Overnight - Swedish Axe, Canvas Lavvu, Wool Blanket
- Saving Our Off Grid Cabin in the Woods (TOTAL RE-BUILD)
- Bushcraft Camp with my Dog - T-Bone Steak on the Camp Fire (SHOW US YOUR STEAK CHALLENGE)
- Cooking at the Off Grid Cabin in the Woods - Woodstove, Firepit (WINTER PREPARATION)
- Camping in a Debris Shelter (Bushcraft) - Lanterns, Log Bench, Deer Hide Beds
- Bushcraft Camp Update 17 - Stone Fire Pit, Cooking, Knife Sharpening (SPIDERS)
- Camping Overnight at The Bushcraft Camp & Off Grid Cabin in the Woods
- Bushcraft - Duck, Flint and Steel, Traditional Gear (Field Sports)
- 20 Minute Bushcraft Shelter (REAL TIME)
- Bushcraft Camp with a Subscriber - Deer Meat, Axe, Knife, Camp Food
- Bushcraft Camp: Full Super Shelter Tour (Tower, Ladder, Shelter, Roof, Log Store, Raised Bed)
- Off Grid Log Cabin with Moss Roof - Cruck Frame Shelter (Overnight Camp)
- Goodbye Bushcraft Camp. WE ARE DONE.
- 2 Day Bushcraft Camp in a Tipi Shelter - Woodstove, Deer Hides, Axe (Camp Craft)