Making the Packable Draw Knife
Description
http://www.selfrelianceoutfitters.com
http://astore.amazon.com/davecante-20
Dave Canterbury, David Canterbury, The Pathfinder School,Bush Craft ,Survival skills, Historical Lore, Primitive Skills, Archery, Hunting, Trapping, Fishing, Navigation, Knives, Axes, Fire, Water, Shelter, Search and Rescue
Tags: Bushcraft,Survival,David Canterbury,Dave Canterbury,Pathfinder,The Pathfinder School,Archery,Hunting,Fishing,Camping,Primitive Skills,Fire,Water,Shelter,Navigation,First Aid,Search and Rescue,Signaling,Prepper,Preparedness,Self Reliance,Survivability,The 10 C's,Knives,Axes,Saws,Bow Drill,Ferrocerium Rod,Ferro Rod,Tarp,Hammock,Canteen,Cooking,Longhunter,Trapping
Video Transcription
morning guys I'm Dave Canterbury with self-reliance Outfitters in the Pathfinder school what I thought I'd do today is walk you through the process of how I make a packable draw knife as a production tool that we're going to be able to sell on our website and I've been developing these packable draw knives for a long time and hand forging them just one here and there and I've sold a few of them just some people I've given a couple of them away I've got a couple of myself and a lot of people are asking for these things and they want to purchase them from our website well something that's hand forged that takes an hour or two to make is pretty difficult to sell if you're trying to make anything for your time and labor so you've got to figure out some ways to shortcut that and that's the way production companies that make tools can sell tools at affordable prices that are made in the US so what I've done is I've given a drawing of a packable draw knife to my father who has set it up with our water jet company to water jet these out of 1095
so I'm getting them as a blank form in 1095 and now I'm going to show you how I turn this blank into a workable draw knife that can be sold to the public and we're hoping for right around $30.00 mark stay with okay so here's a pretty up-close look at the blank itself for you guys
water jet leaves some ridges on things during the water jet process so the first thing I'm going to do is I'm going to kind of knock those off or most of them off and then I'm going to clean the rust off of it where it's been sitting outside and collected surface rust from oxidization it says high carbon steel 1095 then I'm going to go ahead and close these loops down and that may be a change that we make in the designs I may have them already closed down I don't ever want them to be a solid hole without the ability to move because I may decide to change the design or I may find out something works better than something else I may want to use the same design and bring this down straight to be able to put handles on this thing there's a lot of things I can do with this design as it stands so I don't ever want to close that but for now what I have been doing and here's one that's in process right now that just came out of heat-treat I'm closing the loops and then creating my 25 degree bubble on one side and then heat treating them and then doing the final finish so let's take this one and talk about the entire process alright so the thing I do is again I just knock those ridges off I do that pretty quickly and then I knock the ridges off on you sauce another level and spring that out to a flat grind and then I do the boys odd just make sure that that is I try to get nice straight flat I want to get rid of all the bump because that's my lead edge okay now I'm going to just take a sanding block and knock the surface rough off of the Sun reflect up and then just use a hammer on the anvil to close these two eyes while still in an anneal and soft state now once I've closed that up I've got a jig set up here that has a 25 degree bevel angle on it with just a couple of screws wood screws to hold this thing where I want it for the initial grinding process and I just try to make sure that I've got an even amount sticking up above when I get this thing screwed down it's going to stay screwed down and this jig until I get ready for the initial heat treat anyway then I'm going to come in here on a belt
now because I'm removing lots of material very quickly I have to continuously cool the workpiece so I'll grind it
then I'll come in and cool it and then go back to grinding you
remember that this is pretty much a single bevel grind on a draw knife with just a little bit of a micro bevel in the backside and it's 25 degrees is what I found works the best for this so we'll just continue to remove this down to where we get down to about a sixteenth of an inch here and then I get back to you
so what I'm doing now is I'm avoiding turning this material blue and trying to get a nice level grind across the speed okay so I don't want to take this down too far on this edge I want to leave myself about 1/16 because when I heat treat it if the edge is too thin it's going to become weak so the important thing now is to give myself just a little bit of meat left on that piece before I heat treat you now we're going to remove it from the jig take it over to the furnace to the propane flame and we're going to heat treat it turn on the gas heater up get over here run on a baguette agitated quench for about two minutes okay so now we've got it out of the forge we have cooled it and now it is hardened okay we have hardened it with the heat treat process if we wanted to make this metal softer and we are making a knife blade or something like that we want to temper it next and heat it up to a certain temperature and leave it at that temperature for a certain amount of time like 425 degrees for two hours for like a knife blade but because we're making more of a chisel type tool we want this to be very very hard and to hold an edge for a long time so we're not going to temper this blade at all the heat treat is enough we'll have a rockwell on this blade somewhere probably between 60 and 65 as is we've got this metal pretty much as hard as it can get without quenching it in water so we've got what we want here now we got to put it back on the jig and do our final grind and that's why we left ourselves some meat so when we do our final growing down to our cutting edge and our micro bevel we have some meat to work with there okay so again as I'm degree down the jig I'm making sure that I've got even amount sticking up above the jig and this is an actual knife jig but just repurposed for these draw knives and now we're ready to do our final drawing which is a very similar process
we just have to be much more careful now not to heat up the blade and turn it color
we'll remove most of our forging mark to get up to a shiny now I'm walking these far because when they start to jump over the blade or bounce off the top of the blade I know I'm getting thin they're not going in between anymore
so I know that my blade is it's Indus that I needed especially right in here I've got a little area sticker here so I'll give that a little bit more attention until I get to sparks jumping over the top of the blade there you can see that happening right there that's getting my blade exactly where I want there's a little bit of finessed enough for sure okay so once I've got that blade to where I want now I'm going to take it off the jig and from here I'm going to freehand the micro bevel on the backside take out one screw and that will release it from the jig that screw back in there so I don't lose it put that aside and now I'm going to come in here and turn the blade up on end and just freehand a very small micro bevel and it's pretty straight up and down angle
on the back of this blade we can just barely even see it that's exactly what I want
once I get that then I'm going to feel for that
Caroline burrow on the boy not even really pushing this against the platen I'm very early touching it for that micro-velvet
feeling for that bird feeling for that wire edge when I feel that they're not going to take it over to the buff now we're going to bring this tool over to the buffer a little bit of white compound on there get the leading edge first
flip it over roll that bird back and feel my edge at that point I should be pretty sharp without having to much of anything else I have to I've wiped a tool off with an oily rag every one of these tools gets tested
that's a nice draw knife right there beauty okay folks alum Dave Canterbury with self-reliance out there in the Pathfinder school I appreciate you joining me today I heard the Pathfinder Forge and the Pathfinder school classroom for a quick video on how I make the Pathfinder packable draw knife that we will be selling soon on our website I've got about twelve or fourteen of these finished and ready to go to SRO I've got another 50 blanks that just came back from water jet at SRO to pick up to bring out here to have my son finish up of work on so we'll be trickling this into our web site as we can but I wanted to show you the process of how these are made and how they're tested and what the finished product looks like on the video today I appreciate your views I appreciate your support thank you for everything you do for our school for our family for business all of our sponsors instructors affiliates of friends and I'll be back with another video as soon as I can thanks guys
About the Author
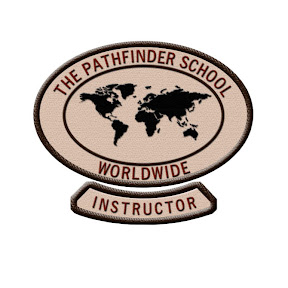
wildernessoutfitters
From the lore of bushcraft to all things related to self-sustainability, the Pathfinder vision is to pass on the knowledge of outdoor self-reliance. Providing basic to advanced self-reliance training and survival gear, our goal is to offer both practical knowledge and survival gear that will stand the test of time. From emergency preparedness to sustainability, the Pathfinder way is to share and educate.
Here you can explore the world of survival knives, survival kits and simple tips on outdoor self-reliance. We are always learning and enjoy passing on the knowledge we acquire.
There is no substitute for having a plan in the event of the unexpected.
More articles from this author
- Black Drawing Salve
- Pace Counting and Dead Reckoning
- Bullet Proof Bushcraft on a Budget Long Guns
- The Witchery of Archery Part 3 Arrows and Arrow Flight
- Sling Bow Final Modification How To
- Journal of the Yurt 29 Q&A
- African Bird Trap
- Journal of the Yurt 37 Stock and Trade
- A Common Man Sustainability Cross Bow
- Modular Packing Discussion
- Rendering Birch Oil, As taught at the PF Pioneer Class by Joe Kellam
- Modern Trapping Series Part 41 Raccoon caught in a False Drain Set.wmv
- Shooting the Recurve Bow (Beginners) with Iris Canterbury.wmv
- Journal of the Yurt 2
- Journal of the Yurt 7
- NINJA SHELTER
- Spring pole Bowdrill Ember
- Cooking Tips and Quick Treats (Garlic Rice and Smoked Sausage)
- 5 Navigation Techniques Every Woodsman Should Know
- Building a Discount Bushcraft Kit Part 5 (Wool Blankets)
- Journal of the Yurt 38 A day in the Life
- Trail Tarp Set up Options Part 1
- Cast Iron Cooking Part 2 Pork Mash Cassarole
- Creating a Fire with Aspen Punk wood and the Sun
- Modern Trapping Series Part 44 Skinning a Mink
- Shoes a Simple Improvised Pattern
- Pathfinder Advanced Class Florida Everglades
- Blacksmithing Part 14 Making Nails
- Bow Saws, a Common Man Bush Tool
- Bow Fishing Equipment Explained
- Kid Testing of the Lightning Strike Fire System
- The Osage Bow Part 6 (Draw Wt and Shooting)
- Modern Camp Set up
- Utilizing Resources Tallow Making Lye Soap
- Apache Foot Trap
- H&R 12 GA Buttstock Mods
- The Quickie Poachers Camp.wmv
- Blacksmithing Part 7 Making Cooking Irons
- Tablet Weaving
- 21st Century Longhunter Processing Tinder Fungus for Use
- Neolithic and Ancient Roman Fire Methods
- Eastern Woodland Trees and their Uses 1
- Using a Compass to take a Visual Bearing
- Journal of the Yurt 24
- Journal of the Yurt 36 12GA R&D
- Kit Mentality the Basics
- Blacksmithing Part 11 Forging a Knife Step 1.wmv
- Beginners Knife Safety Part 1
- Commercial: Dave Canterbury "Makes fire with his beard"
- Modern Trapping Series Part 23 Skinning the Catch
- Starting your net
- Wood Craft on a Budget Part 6 Cookware 2
- Jam Knots 3 that do it all
- Slingshot Forging
- Pathfinder Product Review 11 Flint Knapping Tools
- On the Waters Edge Part 4 Sling Spear
- Pathfinder Product Review #3 The Emergency Shelter Kit
- Pathfinder Product Review #5 The Nessmuk Hand Axe
- Throwing a Knife
- Packable Draw Knife and a Simple Vise for the Woodland Projects
- Bushcraft Kit Shot Show Intro
- Shooting Vanes from a Traditional Bow
- Journal of the Yurt 1
- Testing a Common Man's Survival Bow.wmv
- Diary of the Tipi 4 Primitive Archery Repair Kit.wmv
- ROKON Series Intro
- Cornish Hen Cassarole in an Aluminum Dutch Oven
- Super Shelter Modified for the Eastern Woodlands Part 1
- Improvised Zip Lock Compass.wmv
- 21st Century Longhunter The Versatile #110 Conibear
- Journal of the Yurt 31 Folders and MT's
- Condor Greenland Axe Pathfinder Product Review #12
- Packing for a Trip the 3 C's Concept
- How to get your pattern for a wool blanket shirt
- Brain Tanning Hair On Part 1
- SlingBow DVD
- Fleshing hides: The easy way
- Butcher Knives a Frontier Standard.wmv
- Reviewing a Survival Shotgun Set up.wmv
- Long Guns, Canoe Guns&Testing the Wax Slug 12 GA Load
- Stronghold Haywire Klamper Projects
- Asian Monitor Trap
- NO FAK First Aid Kit
- Journal of the Yurt 6
- Walnut Blueing an H&R 12GA
- Modern Trapping Part 4 Foot Hold Traps
- Mora Camping Axe "Dont save it for the wimpy wood!"
- Quick Run Down of the Final 5 C's of the 10 PC Kit
- 1751 Belt Ax Kit Project Part 2
- Fire Tube
- Journal of the Yurt 28 Spices
- Journal of the Yurt 26 My Shooting Bag
- Utilizing Resources, Glass Arrow Heads
- Iris Intro1.wmv
- PF Cook System for 2017
- Primal Gear Unlimited Compact Folding Survival Bow
- Corn Meal Mush
- Journal of the Yurt 9
- Emergency Fire-Foul Weather
- Boot Care and Boot discussion
- Pathfinder Pocket Hunting System Promo
- Auger Adapter DIY
- Making a Scrap Yard Folding Knife Part 1
- Bug Dope
- Tools and Honing Discussion
- Pine Sap Accelerant
- Journal of the Yurt 5
- On The Waters Edge Part 8 Fileting a Fish
- American Mod to the Asian Bird Trap Snare
- Modern Trapping Series Part 26 Prepping the hide for Tanning
- Modifying Brass Shotgun Shells to accept the 209 Primer.wmv
- Survival Bows (Shaping and Floor Tillering the Stave)
- Woodcrafters Bench Part 4 Spoon Mule Attachment
- Pathfinder School Self Reliance Projects Update 2
- Char Cloth and Ignition Sources
- Wool Blankets Winter Camping Part 2
- Making Woodland Furniture The Dove Tail Joint Lash
- Fire School Part 9 Bowdrill Ember from Horsehoof Fungus
- American Yurt at the Pathfinder School Intro
- Journal of the Yurt 3 Making Hard Tack
- Cast Iron Cooking Part 1 Spicey Rice Dish
- Pathfinder Nessmuk Trail Tarp by Duluth Pack Co
- Take Down Bucksaw Project Wood Craft on a Budget Part 19
- 5 Min Shelter Option Double Wedge
- Swing Arm Cook System from Natural Materials
- Stump Anvil Improvements The Clave
- Throwing the Tomahawk
- Making Corn Flour Cereal.wmv
- Diary of the Tipi 8 Making Gourd Containers Part 1
- Starting Fire with Steel Wool and Ferro Rod
- NEW Gen 2 Small Bushpot
- Exploring the Whelen Lean Part 2
- Converting Your Percussion Cap to 209 SG Primer Ignition (Mag Spark)
- Over Night Scout
- Pathfinder Cribs The Pathfinder Yurt
- Survivability vs Sustainability.wmv
- Self Feeding Fire Part 1 Basic Bushcraft
- Simple Machines 3 Rope Spinner
- Bullet Proof Bushcraft on a Budget Cover
- Wood Craft on a Budget Part 10 Refurbishing Old Tools1
- Survival Basic Series DVD Part 5
- Pathfinder Product Review #14 New Mora Knives
- Addressing Snake Bites
- Top 5 Medicinal and Useful Plants of the Eastern Woodlands Part 1.wmv
- Poplar Dough Bowl Part 1
- Simple Camping Plow Points Part 1
- Clothing for the Cold
- Frontier Fire Methods 2.wmv
- Fishing Kit-Improvments Testing
- Modern Trapping Part 5 Intro to Snares and Snaring
- Equipment List Discussion for Pathfinder Basics
- Processing Small Game Pheasant
- Evolution of Survival
- Black Smithing Part 1 Making a quick Fire Striker from a File
- Modern Trapping Series Part 33 Using PVC in Sets
- Journal of the Yurt 8
- Journal of the Yurt 4
- Introducing the Pathfinder Scout Hawk
- Mini Inferno NEW PRODUCT
- The Common Man's Last Shot- Pocket Pistol
- Scout about and Bacon out
- Simple Bucket Pack Modification
- Navigation by Terrain Feature Association Part 1
- A Quick Bait holder for Catfishing
- Building Traps without Tools
- Journal of the Yurt 27 Securing More Meat
- The Witchery of Archery Remake Part 1 The Two Tracks Long Walker
- Pocket Hunter A Comprehensive Look at Design and Use
- Practicing Fire Methods 1
- Cabin Fever Part 20 Preserving Game meat in Winter
- Cast iron Cooking Part 3 Deep Fried Bass Filets
- Journal of the Yurt 50 Forging a Cookset.wmv
- Journal of the Yurt 23
- Tarp Setups and Research for System Development
- 5x5 Bushfit Kit
- A Review of 3 Pocket Tools
- Bushcraft Tools Fire Piston Test
- Sunfish Lunch'en
- Knapping a Quick Stone Point from a Flake.wmv
- PVC Bait stick Trap
- Bullet Proof Bushcraft on a Budget Containers
- Cooking Squirrel and Rice
- The Spider Shelter Part 3 Finishing up and heating it up!
- Fire School Part 14 Rub Cloth
- Journal of the Yurt 20
- Journal of the Yurt 18
- Journal of the Yurt 41 Pack Goat
- Materia Medica Yarrow 3
- Building a Discount Bushcraft Kit Part 4 (Take Down BuckSaw for Ten Dollars)
- 5 Tools and Functions to manipulate Wood
- Brain Tanning Hair On Part 3
- Grand Opening Invite
- Common Man Self Reliance Bow #2
- Cabin Fever Part 29 ATV Scouting and my Kit 1
- 21st Century Longhunter Mentality and the 5C's
- NEW Council Tool Woodcraft Pack Axe
- 2 Dollar Knife and Sheath Project Part 1
- Reproducing an Antique Draw Shave Part 1
- Basic Multi Use Knots
- New Sling Bow
- Quick Fishing Kit from Common Materials
- Asian Trail Spring Trap
- Natural Cordage Part 2 The Process of Reverse Wrap 2 Ply Cordage
- Ignition Sources, My Belt Kit
- Bushcraft Kitchen Part 1
- Dressing for Cold Weather.wmv
- 5 Minutes to Better Bushcraft Building a Friction Fire Ember
- Torture Test of a Savotta Pack
- Wisdom of the Wall Tent Part 4 Junk on the Bunk
- Full Circle
- Carving a Noggen
- Canvas Ship Hammocks and Weaving a Clew
- Traditional Japanese Water Stone Sharpening
- 5 Minutes to Better Bushcraft Dakota Fire Hole
- Blacksmithing Part 39 Making a Portable Pit Forge
- Dream Hammock System
- Starting Fire with a Compass K&R Alpine
- 5 Wooden Tools
- New Jon Pack Woodsman’s Bed Sleeve
- 5 Minutes to Better Bushcraft proofing and Reproofing
- Mushroom and Plant walk in Sweden
- Mora Adventure 2018 Short clip
- 5 Min Fire and Shelter Conversion.wmv
- Trap Comparison and Thought Process, Modern Trapping Series Part 43
- Simple Fencing
- Rendering and using Raccoon Fat
- Viking research
- Hickory Resources
- Bushpot Chicken and Dumplings
- Woodcrafters Bench Part 2
- 21st Century Longhunter The Oil Cloth Watch Coat
- Game Hooks
- Bill Hawk
- Pathfinder Product Review The JW Trekker
- Basic Camp Overnighter Part 3
- Next Fire Mentality
- 50 Dollar Tool Kit for Green Woodworking
- Pathfinder Product Review #6 The Duluth Pack PF Haversack.wmv
- Steam Bending Wood
- Water Filter Comparison
- Sling Bow (Bow Fishing Mod How To)
- Survival Bow Making(Making a Bow String)
- Making A Common Man's Broadhead
- Building a Discount Bushcraft Kit Part 7 (The Blanket Pack)
- Exploring the Whelen Lean
- Blacksmithing on a Budget
- Building a Discount Bushcraft Kit Part 6 (Cheap Small Game Snares)
- Materia Medica INFUSIONS The Woodsman's Expectorant 22
- Fire School Part 8 No Container Char
- Norlund Axes
- Using Flex Seal on a Canvas Pack
- Pathfinder Product review #4 The Pathfinder Trade Knife.wmv
- Knives and Processing Wood
- Axes and Hatchets Wood Craft on a budget Part 15
- Opinel Safety Mod and Penny Knives
- The M44 Mosin Nagant, A Common Man Rifle
- Simple Box Traps Live Rabbit Box
- Grass Thatching
- Frontier Fire Seminar from the Camping and Woodcraft Class
- Rocky Woodland Forge's Woodcraft Tool Kit
- Stack Pack by Short Lane Arms
- Restoring A Scrap Yard Wood Stove
- Diary of the Tipi 10 I love Fire! my EDC.wmv
- PFODJ Ep4 18th Century Woodsman Hunters Camp
- Camp Cookery Baked Rabbit
- Survival Pro Tips 1 Making Fire with an Empty Bic
- Simple Box Traps Mink Box
- Fire School Part 2 Bow Drill Lessons
- Meat Processing Tools
- Fire School Part 7 Strikers, Scapers, and Smooth Strokers
- Tools and Wood Processing
- Medicinal Trees of the Eastern Woodlands 1.wmv
- Hush Puppies on the trail
- Blacksmithing Part 17 Scrap Yard Pick'en
- Hammock Chat
- Knife Making , Material Reduction Knife Start to Finish Part 1
- Belt Pouch EDC
- Useful and Medicinal Trees of the Eastern Woodlands 3
- Using the H&R 12GA for a Muzzeloader
- Ultimate Survival Bows
- Journal of the Yurt 11 Hygiene
- Journal of the Yurt 10 Visit with Jeremy Janey PF School Intructor
- On the Waters Edge 13 Day 2 Mohawk Canoe
- Hygiene from Fire
- Wisdom from the Wall Tent Part 1
- Making a Common Man Limb Quiver for Hunting
- Coyote Consuming the Harvest
- Knife Care in the Field
- Hobo Stew and Corn Bread
- Bushpot Jambalaya and Hushpuppies
- Useful and Medicinal Trees of the Eastern Woodlands 4
- Basic Camp Overnighter Part 1
- Axe Care Made Simple
- Bulletproof Bushcraft on a Budget Part 1
- Snares The Ugly Truth Modern Trapping Part 57
- Kit mentality Useage vs Investment
- Blacksmithing Part 36 The Wind Tunnel Forge
- New Primitive Technologies Discussion
- Blacksmithing Part 13 Forging a Knife Step 3 Heat Treat and Testing
- Fire Lay The Proper Construction and Ignition after a Night of Rain
- Fire Arms Combination for Long Term Sustainability
- Modern Trapping Part 29 Foothold Pocket Set
- Basic Knife Handling and Bush Craft Notches Part 1
- Blacksmithing Part 18 Making a Brake Drum Forge
- Bucking with a HB Cruiser Ax Wood Craft on a Budget Part 16
- Journal of the Yurt 12
- Reloading 12GA with (Pyrodex) Black Powder in the Field
- Skinning a Raccoon with Rope,Modern Trapping Part 32
- The Witchery of Archery Part 2 The Basics
- Honeysuckle resources and a quick update
- Survival Bows (Collecting the Stave, Improvised Draw Knife)
- Skinning a squirrel for a usable hide
- Blacksmithing Part 12 Forging a Knife Step 2 Material Reduction
- Evolution of the 10 C's Part 1
- Shelter Basic Tarp Setups 1
- Fire The Basic Class Presentation
- Mora Garberg Full Tang Discussion and Review
- NEW 2 1 Ltr Bushpot and 64 Oz Bottle
- Shelter Basic Tarp Setups and an E Fire 2
- Mora Dangler made simple
- Simple Machine Woodland Hoist
- Coyote It's whats for Lunch
- Shelter Basic Tarp Setups 3
- A Woodsmans Apothocary
- Wooden Pulleys and Lifting
- Deer Heart and Pepper Gravy Camp Cooking
- Simple Woodcraft Aids
- Overnight Pack Out
- Fire School Part 1 Bow Drill Lessons
- Collapsible Cast Iron Skillet DIY
- Quick Upload Extracting Pine Tar from Fat Wood
- Blacksmithing Part 15 Making tools for Spoons and Ladles
- Forging and making a Primitive Adze
- Trapping Season Prep and Primer Discussion
- Top 10 Non Firearm Meat Gathering Tools
- Haversack Kit
- Pathfinder Advanced Class 1_7_2010 MA, USA.wmv
- Squirrel Hunt with a Flintlock
- Best Medium Game Snare Modified figure 4 Trigger
- Council Tool Hudson Bay Camp Axe
- Gig Discussion and Hunt with Weapon Vision Spear Cam
- 2 Dollar Knife and Sheath Project Part 2
- Go Ruck Rucker Review and Kit layout
- Bushcraft Breakfast Bannock
- On the Waters Edge Part 1 Compact Fishing Rods and Systems
- Toggle Trigger Fishing Variation
- Swiss Army Knife easy Ember , Fire Tips and Tricks
- Roycroft Pack Frame Part 3 Using Shelter Components
- Blacksmithing Part 4 Rounding and Drawing steel to make a Trap Stake
- Fire School Part 13 Ferro Rod Tips
- Tension Bending Pack Boards
- 12GA Shell Bag Contents and Discussion
- Bushpot Convection Oven
- Stretcher Bed Setup
- Pathfinder Folding Skillet
- Making Sweet Corn Bread Drop Biscuits
- Diary of the Tipi 2 Making Hide Glue.wmv
- Otzi s Knife Sheath
- Pathfinder Basic Survival Class Video Diary
- A Common Man's Grease Lamp
- Canterbury Camp Kitchen
- Rokon Winter Packout
- Blacksmith a Squirrel Cooker explained Part 47
- Leather Knife Scales
- M6 Scout Update Review
- The Osage Bow Part 1
- Basic Carving Kit
- Snow Shoes JMHO
- Simplicity
- Final Product Modified Kephart Bedroll by Duluth Pack
- Swedish Lap Vise
- Forging a Custom Carving Axe with Liam Hoffman Part 1
- Toggles The Woodsmans Friend
- Tarp Setups the Foresters Tent and the 4 W's
- Making a Blade Bowl Adze
- The osage Bow Part 4
- Taking a Bearing from your Map made easy
- Journal of the Yurt 43 Stock and Trade Part 2
- Survival JMHO
- Simple Camping Improved Pot Crane System
- Batoning Wood with your Knife
- Improving the Wax Slug Load for 12 GA and Black Powder Equivelant
- Modern Trapping Part 7 Bedding Foot Hold Traps
- Wisdom of the Wall Tent Part 3 Camp Tool Box
- Useful and Medicinal Trees of the Eastern Woodlands 5
- Pine Crate Tool Chest
- Pathfinder School Basic Class Equipment List Rundown
- Diary of the Tipi 11 Care for a Smoothbore Flintlock.wmv
- Baking with a Plank and a Bushpot
- Wood Craft on a Budget Part 3 Sheath Knives Continued
- Building a Discount Bushcraft Kit Part 3 (Food)
- Triple Barrel Shotgun PF Edition Intro
- Maul a good Learning Project
- Meat Preservation Concerns and Setting Snares
- PFODJ Ep 11 Wet Weather Fire Segment
- The Small Common Man Trapping Kit
- Useful and Medicinal Trees of the Eastern Woodlands 2
- Simple Camping Connection Knots 3
- Pathfinder Outdoor Journal Ep1 FULL HD Episode
- Quick Review of the ILBE USMC Assault Pack and Sealine Insert Bag
- Simple Blade Grinding Jig
- Diary of the Tipi 12 Working with Natural Dyes Part 1.wmv
- PF SS Kettle
- Jeff White Bush Knife and a Wet wood Fire
- My Back Yard
- Knives JMHO
- Iris Intro Video Part 2.wmv
- Thanks for Play'en, Bobcat in an MB 450 Released
- Kit Mentality Updates
- Bullet Proof Bushcraft on a Budget PVC Pack Frame
- The Osage Bow Part 5
- The Mocotaugan
- Pathfinder Knife Shop Introduction
- Deadliest Small Game Primitive Trap
- Saami Repair Kit
- Building a Discount Bushcraft Kit
- Stone and Bone (Utilizing Resources) Part 1
- No Map No Problem Part 2
- Arrow Making for the Common Man
- The Wish Bone Trigger Snare New
- Making a quick Spring Lathe
- Using the Slingshot to Hunt Bigger Game
- Bark Basket Part 1
- Scout Camp Common Man Black Powder Setup
- Collecting Back Sinew and Some Meat from a Roadkilled Deer
- Dakota Fire Hole Proper Construction and Use
- Artifact Quality Leather Work
- Bucket Making White Coopering
- PFODJ Ep 5 Axe Tomahawk Segment
- Reverse Figure 4 Dead fall Trigger
- Fire and Bushpots
- Shooting Shot from a 50 Cal BP Rifle
- Tarp Setups Modifed Plow Point
- 50 Cal Blue Ridge Mountain Flint Lock
- Remington Shotgun Model 1889 Double Barrel
- Shrink Pot 1
- Reflector Oven Bread
- Preping the Sling Bow for a Big Game Hunt
- Modern Trapping Coon in Beaver set
- Brimstone Matches and Next Fire Mentality
- No Map No Problem Part 3 Height and Distance
- Saw Maintenance 2 Wood Craft on a Budget Part 14
- SS Canteen Available NOW!~
- Identifiying Flint Chert and other Sparking Rocks
- Trap Sets The Step Down Set Modern Trapping Series Part 48
- Axe Selection and Use
- The Osage Bow Part 2
- Tomahawk from a Rasp Blacksmithing Part 46
- Making Pemmican
- Moonshine Why Carry
- Trailblazer Deliverables Basic Compass Use
- Making the Flemish Bow String in the Bush Part 2
- Simple Camping Hammock use with Wool Blankets
- Forging a Hook Knife
- Finishing a New Old Stock Mora 311
- Survival Basic Series DVD Part 1
- Sharpening an Axe with a Hardware Store Grind
- Putting a Handle on a Mora Blade Blank
- Simple Machine DIY Spring Hammer
- Forging a Tomahawk from a Rasp
- Feathersticks or Shavings
- 21st Century Longhunter Series Combustion
- Fire School Part 15 Pump Drill Fire,Learning the process
- Seneca Pack Frame
- Ever thought about this? Fire Tricks
- Sustainability Long Term,Modern Trapping Series Part 42
- Blacksmithing Part 2 The Folding Small Game Gambrel
- Double Bit Axes Wood Craft on a Budget Part 17
- Sleeping Gear JMHO
- Knapping Arrowheads From Glass Part 1
- Mora Bushcraft Pathfinder
- Making a Cook Tripod with a Chain
- One Match Fire for BSA Bushcraft
- Rope Bed Construction
- The Spider Shelter Part 4, Simple Improvments
- Quick and Easy Tensioner Knot for your Tarp Lines.wmv
- 10 Simple Knife Projects Part 1
- Lighting a Candle with Flint and Steel
- Winter Pack Out
- Utilizing Resources (Making Venison Jerky) Part 2
- Natural Cordage Part 1 Harvesting and Processing Materials
- Asian Bird Trap Laos
- Vines and Withies
- Woodman's Pal
- Five Tool Rule
- Prefered Clothing and Layering for the Woods
- Simple Shadow Navigation Part 1
- Brain Tanning Hair On Part 2
- R&D of the Kephart Bedroll by Dave Canterbury and Duluth Pack
- Light Weight Scouting Pack Set up
- Trapline Diary Part 1 Coon Cuffs
- Survival Basic Series DVD Part 2
- Pathfinder Basics Estimating Distance and Pace Count Lecture
- Super Shelter Modified for the Eastern Woodlands Part 2
- FULL TANG MORA Bushcraft Knife
- Beginners Knife Safety Part 2
- Survival Bows (The Tillering Process)
- Blacksmithing Part 6 Common Man Tools and lighting the Forge
- Building a Discount Bushcraft Kit Part 2
- Sloyd Project 1 Fid
- On the Waters Edge, Trekken and Fishen
- Traditional Cold weather Hammocking
- Knife Making, Material Reduction Knife Start to Finish Part 3
- Trapline Journal Coyote in MB450
- Winterizing the Hammock for the Common Man
- Samick Sage Recurve 8pt Buck Kill
- Large Bushpot Intro
- Bucksaw Modifications
- Fatwood Collecting Processing Igniting
- Aussie Wool Blanket
- Assembling a Custom Classic in the Mora Factory
- Traditional Camp Pack weight
- PFODJ Ep 2
- Hook Knife Part 1
- Making a Bushcraft Knife Part 4
- 1908 A&F Cook Grate
- Nordic Pocket Saw
- Making a Bushcraft Knife Part 1
- PFODJ Ep 5 Moved from the Pay Channel
- PFODJ Progression of Meat Source Gathering
- Experiments in Viking Navigation Viking Sun Stone
- Turkey Tail Materia Medica
- Hook Knife Part 2
- Making a Bushcraft Knife Part 3
- Making a Bushcraft Knife Part 2
- Double on Coons
- The Woodsmans Pantry Plus and the Woodland Chef Cook Kit
- Cooking Bannock in the Bush Pot with a Pack Grill Rack
- Fence Line Snares for Coyote
- Forged Scissors Part 2
- Forged Scissors Part 1
- Pathfinder Scout Hammock
- Trappers Cabin Season 2 Part 5 Raccoon Meatloaf
- Trappers Cabin Season 2 Part 2 Firearms
- Trappers Cabin Season 2 Part 7 Fleshing Hides
- WInter Clothing Discussion
- Trappers Cabin Season 2 Part 4 Tail Stripping
- Hammock Chair Hunting Seat
- Trappers Cabin Season 2 Part 1
- Trappers Cabin Season 2 Part 6 Single Shot Maintenance
- Trappers Cabin Season 2 Part 8 Pocket Sets
- Making a Holiday Wreath
- Trappers Cabin Season 2 Part 9 Making Kvass
- Trappers Cabin Season 2 Part 3 Trash Panda
- 110 For Mink
- Trappers Cabin Season 2 Part 13 Wood Stoves
- Morakniv Carbon Steel Garberg
- Trappers Cabin Season 2 Part 14 Releasing a Domestic Animal
- Z Drag with wooden Pulleys
- Trappers Cabin Season 2 Part 12 Log Crossing Set
- Trappers Cabin Season 2 Part 11 Chasing Mink
- Exotac Products and Titan Lighter tips
- Trappers Cabin Season 2 Part 10 Mapping the Creek Bed
- Trappers Cabin Season 2 Part 15
- Trappers Cabin Season 2 Part 16 Last day for a few
- Trappers Cabin Season 2 Part 18 Buck Mink
- Trappers Cabin Season 2 Part 17 Hidden Woodsman Pack
- Bushcrafting a Tarp Clip
- DD Tents
- Neck Knife to Carry or Not to Carry
- Blanket Pin Tripod
- Comprehensive Bow Drill
- Hibiscus Cordage
- The Versatile Marline Spike Hitch
- Hammock Chair Terrapin Outfitters
- Sticky Rice
- Udemy Intro Video
- Conserving the Bic in an emergency
- LL Bean Continental Ruck Sack
- Navigation The X Box Exercise
- Cave Man Conibear Updated
- Limb line Hook Set Device from natural materials
- Solar Embers without Char or Fungus
- Packing up the raised Bed Camp
- Raised Bed Emergency Shelter
- Basket Trap for Crayfish
- Making a Sun Compass
- Ottomani Sun Compass
- Dutchwaregear Chameleon Hammock and Xeon Tarp
- Tulip Poplar Knife Sheath
- Shadow Board Direction Finding
- Dirty by design
- Orienting a Map without a Compass
- Mushroom Foraging Part 2
- 5 Minutes to Better Bushcraft Pot Crane
- Paracord Hammock
- 5 Minutes to Better Bushcraft Quickly Deployable Ridgeline
- 5 Minutes to Better Bushcraft Hanging Camp Gear
- Tighten a Shear Lash Easily
- 5 Minutes to Better Bushcraft Tripod
- 5 Minutes to Better Bushcraft 90 Degree Spine
- Mushroom Foraging
- Broiling Fish with Grill Racks and the SRO Monthly Special
- Exerpt on Basket Weaving at the Bushcraft 101 Class
- 5 Minutes to Better Bushcraft Double Prusik Tensioning System
- Week Long Training Loadout
- Lunch and the Base Camp Cookset
- 5 Minutes to Better Bushcraft 5 Navigational Aids
- 5 Minutes to Better Bushcraft The Angular Advantage
- Last Shadow First Shadow Method
- 5 Minutes to Better Bushcraft Improved Fire Starting
- 5 Minutes to Better Bushcraft Pot Hanger
- Tulip Poplar The Best Eastern Woodland Bushcraft Resource
- 5 Minutes to Better Bushcraft Bark Candle Lantern
- Woodsman's Gear of the 20th Century Part 6
- 5 Minutes to Better Bushcraft The JB Figure 4 Variant
- Mushroom Foraging Part 3
- Woodsman's Gear of the 20th Century Part 3
- 5 Minutes to better Bushcraft other uses for Puffball Mushroom
- Woodsman's Gear of the 20th Century Part 7
- Woodsman's Gear of the 20th Century Part 5
- Fried Puff Ball Mushrooms
- Woodsman's Gear of the 20th Century Part 4
- Using a Strop to Clean, Sharpen, and Hone your Blades
- Woodsman's Gear of the 20th Century Part 1
- Best Survival Deadfall Trigger PDF4
- Woodsman's Gear of the 20th Century Part 2
- Woodsman's Gear of the 20th Century Part 9
- Woodsman's Gear of the 20th Century Part 8
- Woodsmans Gear of the 20th Century Part 10
- Woodsmans Gear of the 20th Century Part 11
- Blood Trailing a Deer
- M6 Takedown Rifle Comparison to the Springfield Scout
- Safe Release of Non Target Species
- French Press Testing and Protyping
- Simple Camp and a Test of the Wildward Lavu
- Pocket Stove Comparison